Utensili, Tipologie e Applicazioni
PREREQUISITI
- Conoscenza base dei processi di asportazione di truciolo
- Conoscenza base di lavorazioni CNC
- TEMPO DI APPRENDIMENTO: 60 min.
OBIETTIVI
- Imparare a conoscere le principali tipologie di utensili
- Imparare a selezionare la tipologia corretta di utensile in base all’applicazione
INTRODUZIONE
“Nella tecnologia d’officina, pezzo meccanico di forma, dimensioni e qualità meccaniche adeguate che, usato manualmente o applicato a una macchina, serve ad asportare o incidere il materiale (legno, metalli, pietre, ecc.) dei pezzi in lavorazione, o anche a imprimervi delle deformazioni permanenti.” (Treccani.it – Enciclopedie on line, Istituto dell’Enciclopedia Italiana).
Questa è la definizione che l’Enciclopedia Treccani riporta per la voce utensile. Andando più nello specifico delle lavorazioni meccaniche tale definizione viene incastonata in quella di processo di asportazione. Esso viene definito come una lavorazione in cui un utensile, dotato di moto relativo rispetto alla superficie del pezzo, ne asporta uno strato superficiale trasformando il materiale in truciolo e generando una nuova superfice.
Nella macrocategoria delle operazioni per asportazioni di truciolo sono compresi diversi processi, ognuno di essi atto ad ottenere geometrie differenti: rotazionali, prismatiche o miste. Le lavorazioni principali che appartengono a questa macrocategoria sono:
- tornitura, per la realizzazione di lavorazioni assialmente simmetriche;
- foratura, per la realizzazione di fori;
- fresatura, per componenti prismatici;
- alesatura, per la finitura di cavità cilindriche con tolleranze dimensionali strette;
- maschiatura, per la realizzazione di filettature.
Ad ogni tipologia di lavorazione (foratura, fresatura etc.), operazione (spianatura, contornatura, etc..), condizione di lavoro (elevati avanzamenti, presenza di lubro-refrigeranti, etc.) e materiale da lavorare corrispondono utensili specifici caratterizzati da feature differenti. Alla luce di un così vasto e sfaccettato mondo si è deciso di proporre una panoramica sui tipi di utensili più diffusi nel settore dell’asportazione di truciolo.
Quando si tratta di utensili la prima grande distinzione che si può fare è tra:
- Utensili integrali
- Utensili ad inserti
Tale distinzione fa riferimento alla struttura dell’utensile stesso. Come ne suggerisce il nome nel primo caso si presenta una struttura integrale ovvero unica tra stelo, generalmente chiamato codolo, e zona del tagliente.
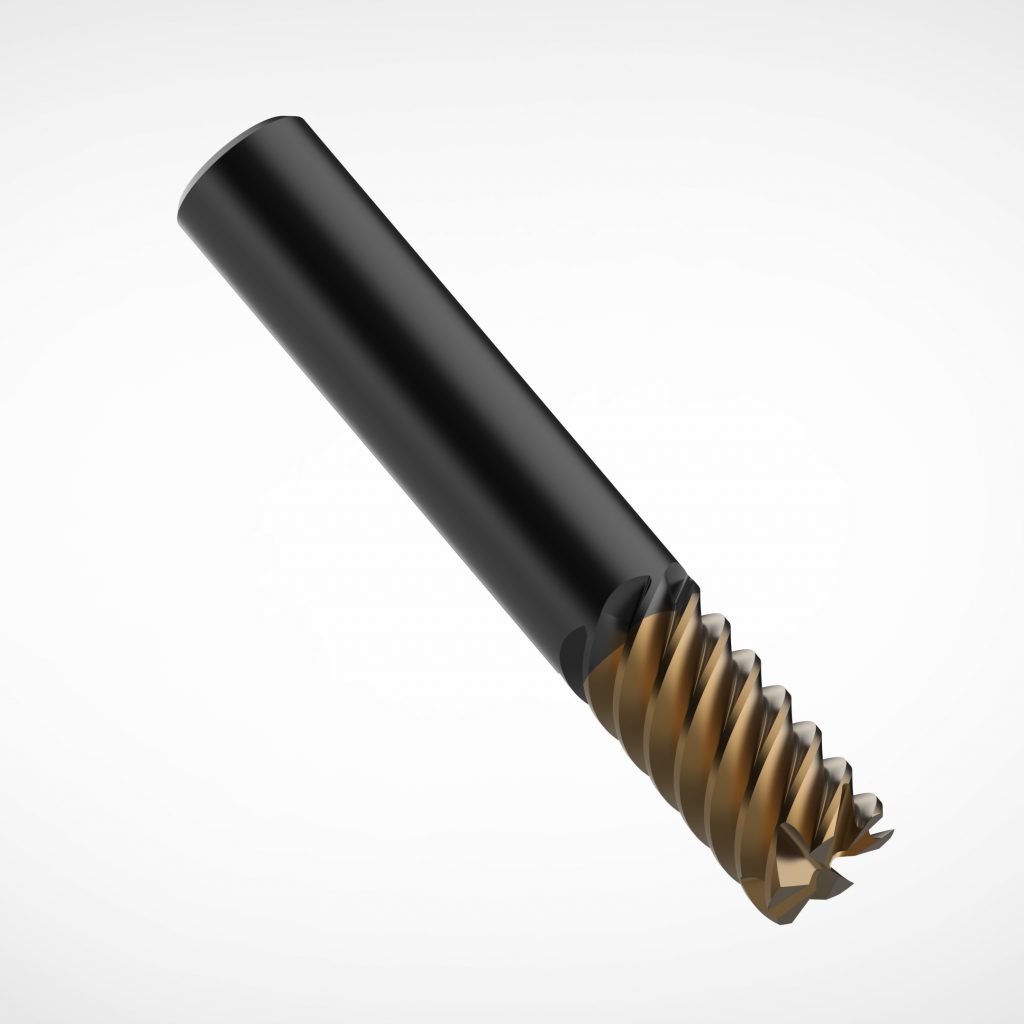
Esempio di un utensile da fresatura integrale
Per quanto concerne invece gli utensili ad inserti, questi presentato una struttura composta da due componenti a sé stanti ovvero lo stelo e gli inserti. Lo stelo ha funzione strutturale e di sede in cui poi vengono applicati gli inserti che si presentano come placchette di diverse forme , dimensioni (specificate nella ISO 1832:2017) e materiale e svolgono la funzione di asportare il materiale lavorato.
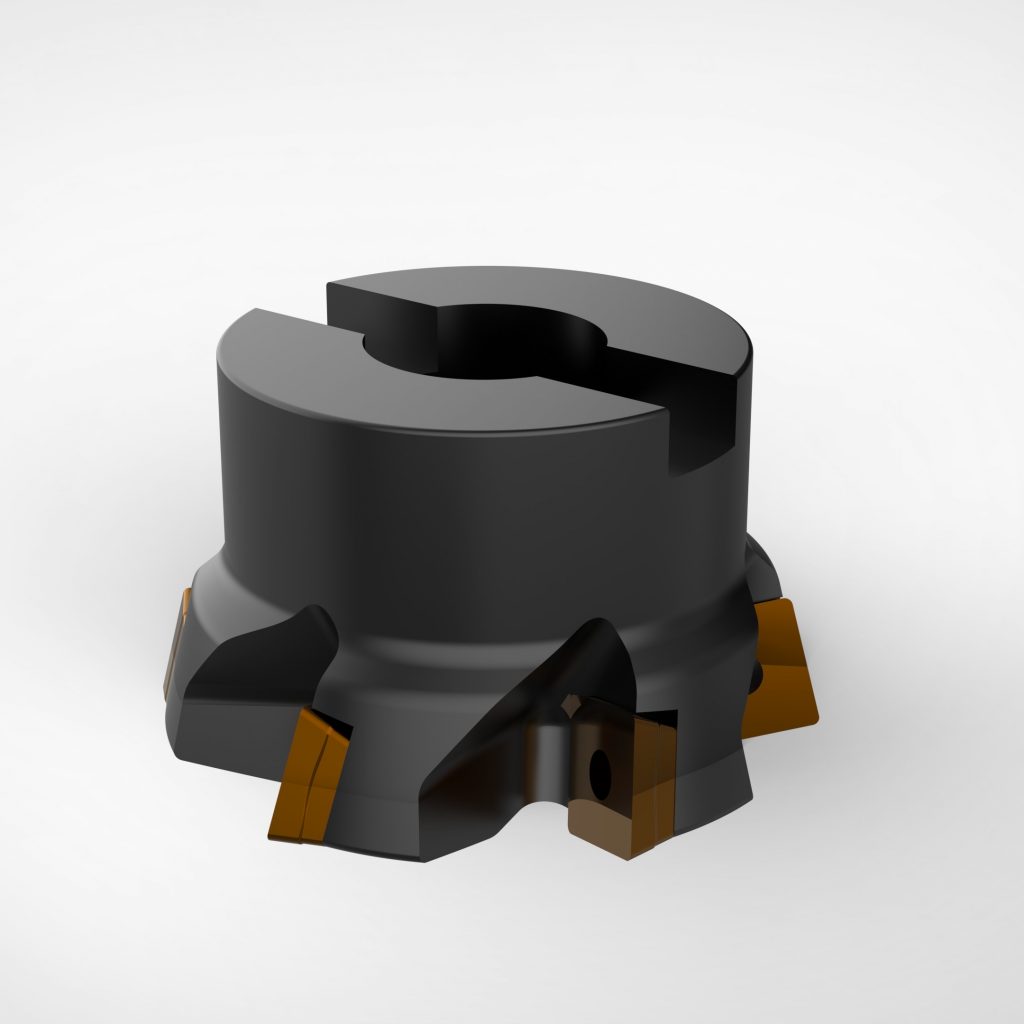
Esempio di un utensile ad inserti
Entrambe le architetture sono tutt’ora largamente impiegate nella produzione, il motivo è che ognuna di esse presenta pro e contro.
- Utensili Integrali – Pro
- Gli utensili integrali consentono di raggiungere tolleranze strette poiché la loro natura monolitica garantisce una precisione dimensionale superiore agli utensili a inserti.
- Ottime finiture superficiali.
- Utensili Integrali – Contro
- Gli utensili integrali essendo fatti di un unico materiale difficile da lavorare, sono costosi da produrre sia a livello di processo che di materia prima, questo comporta un limite superiore alle dimensioni raggiungibili.
- Utensili ad Inserti – Pro
- Gli utensili ad inserti presentano la possibilità di raggiungere dimensioni di gran lunga superiori a quelli integrali.
- Gli utensili ad inserti permettono un impiego più efficiente del materiale da taglio impiegandolo solo negli inserti e non per l’intera struttura.
- Possono raggiungere velocità di avanzamento maggiori e di conseguenza un tasso di rimozione del materiale (MRR) superiore.
- Utensili ad Inserti – Contro
- Hanno una fonte di incertezza maggiore dovuta al posizionamento dell’inserto nella sede, di conseguenza non sono in grado di ottenere tolleranze comparabili agli utensili integrali.
- Impossibilità di raggiungere diametri piccoli poiché sotto ad una certa soglia il fissaggio dell’inserto allo stelo diventa poco efficiente se non problematico o addirittura impossibile. Generalmente questa soglia si attesta attorno ad utensili dai 12 mm di diametro.
- Utensili Integrali – Pro
UTENSILI INTEGRALI
In questa sezione vengono descritte diverse tipologie di utensili integrali:
- Fresa a candela piatta
- Fresa torica
- Fresa a testa sferica
- Punta a forare
- Alesatore
- Utensile da maschiatura (maschio)
- Broccia
FRESA A CANDELA PIATTA
La fresa a candela piatta è una delle tipologie di utensile più versatili presenti nel panorama della fresatura. Esistono molti tipi di frese a candela. Quella piatta è caratterizzata da profilo squadrato e dunque presenta un angolo di 90° tra i taglienti laterali e quelli della testa. Il raccordo tra i due taglienti infine presenta uno smusso più o meno pronunciato per distribuire le forze di taglio più efficacemente e prevenire un’usura precoce del tagliente in corrispondenza dello spigolo. Grazie alla geometria cilindrica e alla presenza di taglienti sia lungo i lati che sulla testa, permette di rimuovere materiale sia in direzione radiale che assiale e dunque di eseguire operazioni sia in sgrossatura che finitura di contornatura, spianatura, foratura con strategia elicoidale e realizzazione di tasche. Il numero di taglienti è variabile e generalmente può andare da due fino a un massimo di otto ma ci sono anche casi con geometrie mono tagliente o addirittura con numero di taglienti superiori a otto ma che rimangono circoscritte ad applicazioni particolari.
Il numero di taglienti dipende principalmente dal materiale per cui è stata concepita la fresa e dall’applicazione. Lo scopo è sempre quello di evacuare il massimo volume d truciolo possibile. Per quanto riguarda le dimensioni di massima invece tali frese possono presentare diametri di 0.2 mm fino a 25 mm circa, anche in questo caso ci possono essere eccezioni che esulano da tali dimensioni. Data la sua versatilità questo utensile da fresatura è molto utilizzato nell’industria manufatturiera odierna.
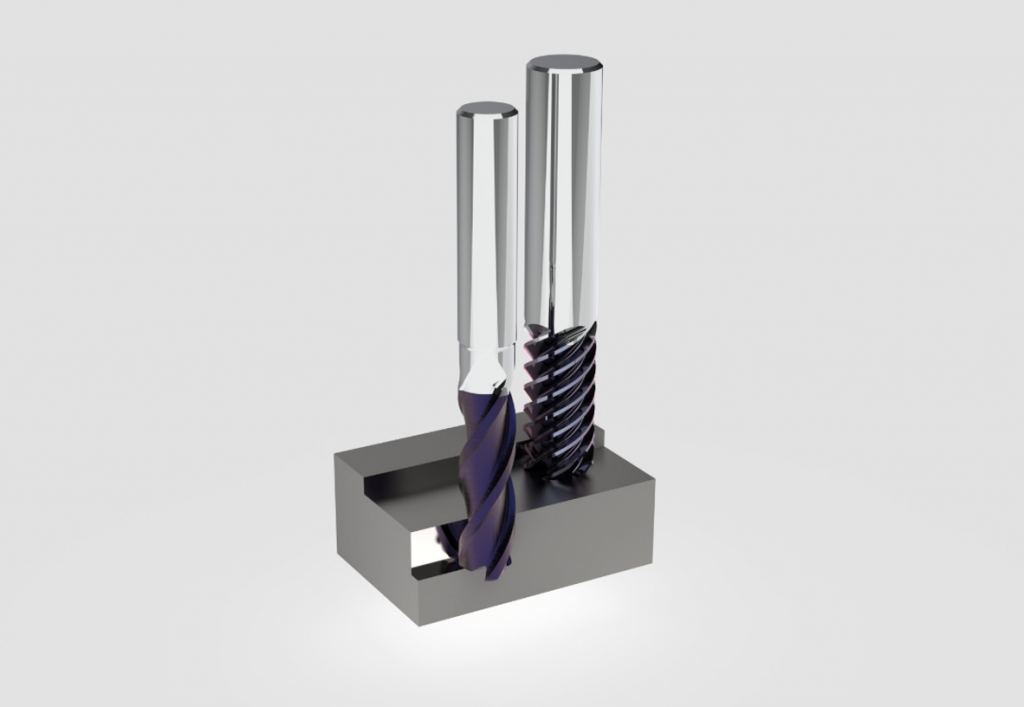
Esempio di una frese a candela piatta con due numeri di taglienti diversi (3 e 8 taglienti)
FRESA TORICA
La fresa torica è una fresa a candela simile sia geometricamente che dal punto di vista applicativo alla fresa a candela piatta. La principale caratteristica che differenzia una geometria torica da quest’ultima è la presenza dello spigolo raggiato sul fondo dell’utensile che conferisce al volume spazzato dai taglienti la caratteristica forma torica. Questa scelta costruttiva consente di ottenere un tagliente dalla sezione più resistente agli sforzi derivanti dal taglio permettendo avanzamenti maggiori. Un’altra caratteristica di molte frese toriche è che sono “scaricate” al centro, questo vuol dire che il tagliente sul fondo della fresa non arriva fino al centro di rotazione, questo è parte dell’ottimizzazione della fresa poichè si elide la componente di tagliente che asporta materiale a più bassa velocità di taglio. In questo caso, l’utensile non può penetrare il materiale assialmente senza un pre foro. La geometria raggiata è usata nelle fasi di sgrossatura nelle lavorazioni di spianatura e contornatura.
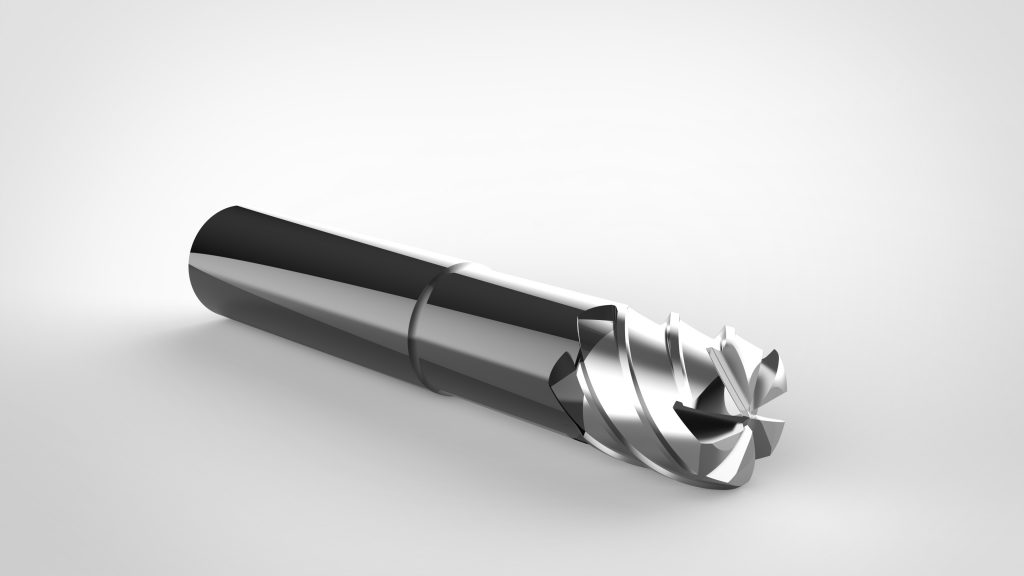
Esempio di una fresa torica a 4 taglienti
FRESA A TESTA SFERICA
La fresa a testa sferica presenta una testa semisferica con raggio pari a quello della fresa stessa. Come nel caso precedente la rimozione di materiale può avvenire sia in direzione radiale che assiale. A differenza della candela piatta sul mercato sono presenti fresa con testa sferica con meno taglienti. Generalmente le geometrie comprendono 2 o 4 taglienti. Data la versatilità di movimento nel materiale e la possibilità di orientare l’asse di rotazione più liberamente e quindi di controllare l’arco di contatto (generalmente si inclina l’asse in modo da massimizzare la velocità di taglio), questa fresa permettere di realizzare operazioni di contornatura, profilatura e copiatura di superfici complesse da lavorare con altre frese (superfici free-form o raggiate).
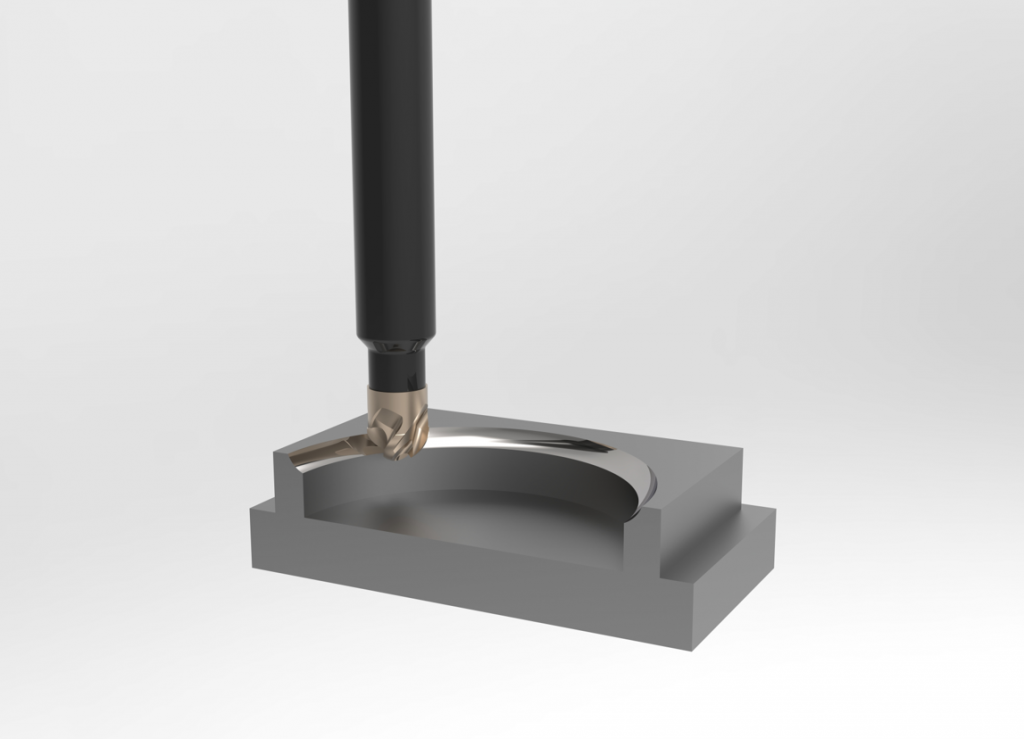
Esempio di una fresa a testa sferica
PUNTA A FORARE
Come suggerisce il nome, questo utensile è impiegato per le operazioni di foratura. La geometria utensile più utilizzata è quella elicoidale. Questa geometria è descritta come un corpo cilindrico in cui sono ricavate delle scanalature che hanno lo scopo di facilitare l’espulsione del truciolo venutosi a formare in fondo al foro in presenza dei taglienti primari. Ciò che rende la punta a forare specifica per questa operazione è la presenza dei taglienti primari sul fondo e ciò comporta la rimozione del materiale unicamente in direzione assiale permettendo la creazione di fori di diametro pari a quello dell’utensile.
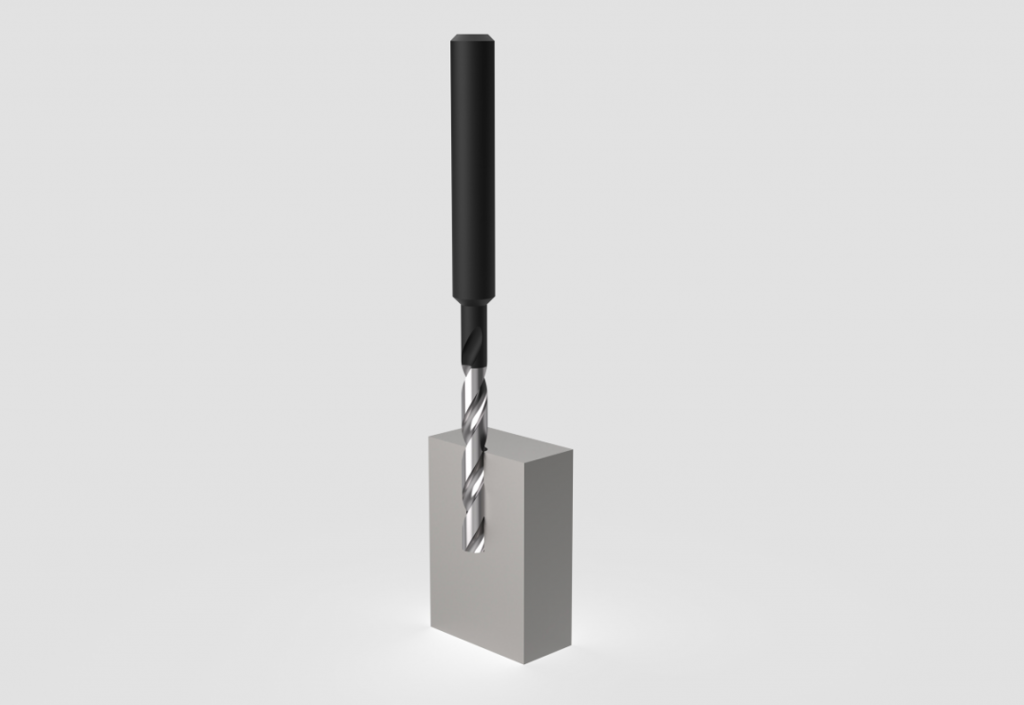
Esempio di una punta a forare
La lavorazione di fori in materiali difficili e/o profondi è necessari la lubrificazione in situ del tagliente. Tale azione è necessaria per due motivi principalmente:
- Facilitare l’evacuazione del truciolo
- Raffreddare la zona di taglio
Per fare ciò la lubro-refrigerazione può essere addotta esternamente tramite i cannelli esterni della macchina utensile o internamente, ovvero, attravaerso dei canali ricavati all’interno dell’utensile il cui compito è quello di fornire il lubrorefrigerante in fondo alla feature in lavorazione. Nei casi generali l’utensile da foratura presenta due taglienti ma ci possono essere casi con un numero maggiore (3 o 4 taglienti).
ALESATORE
L’alesatore è un utensile nato per la fase di finitura dei fori. Generalmente è di forma cilindrica con la parte finale di forma conica per facilitare l’imboccatura dell’utensile nel foro e portarlo gradualmente in misura. I taglienti sono paralleli all’asse dell’utensile o tuttalpiù inclinati. Essi vengono impiegati per la realizzazione di fori in cui poi andranno ad alloggiare spine o altri componenti richiedenti una grande precisione dimensionale e di forma (ad esempio fori con tolleranza H7).
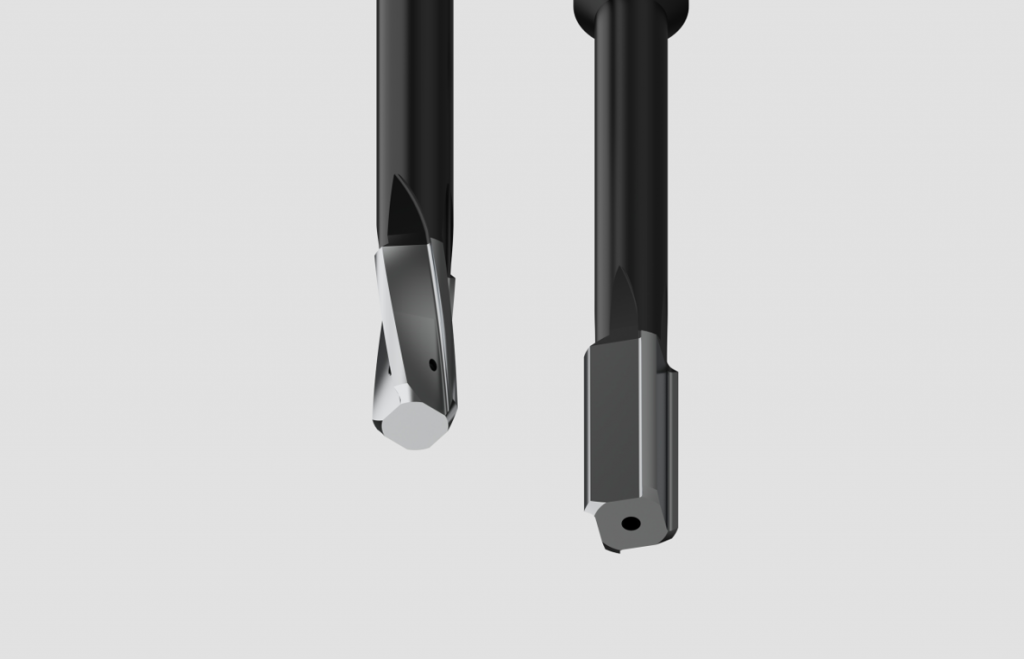
Esempio di due alesatori con taglienti inclinati e dritti
BROCCIA
La broccia è un utensile utilizzato per la realizzazione di profili interni o esterni di particolari geometrie con elevata precisione. Generalmente l’utensile è formato da uno stelo popolato in direzione longitudinale da denti che aumentano progressivamente di dimensione fino a raggiungere la sezione che deve avere il profilo designato.
La prima grande e più generale distinzione che si può fare nella famiglia delle brocce è quella tra broccia a trazione e a compressione.
- La prima tipologia, a trazione, si ha che la forza necessaria a tagliare il materiale è applicata a valle del profilo di lavorazione.
- La seconda tipologia, a compressione, la forza è applicata a monte
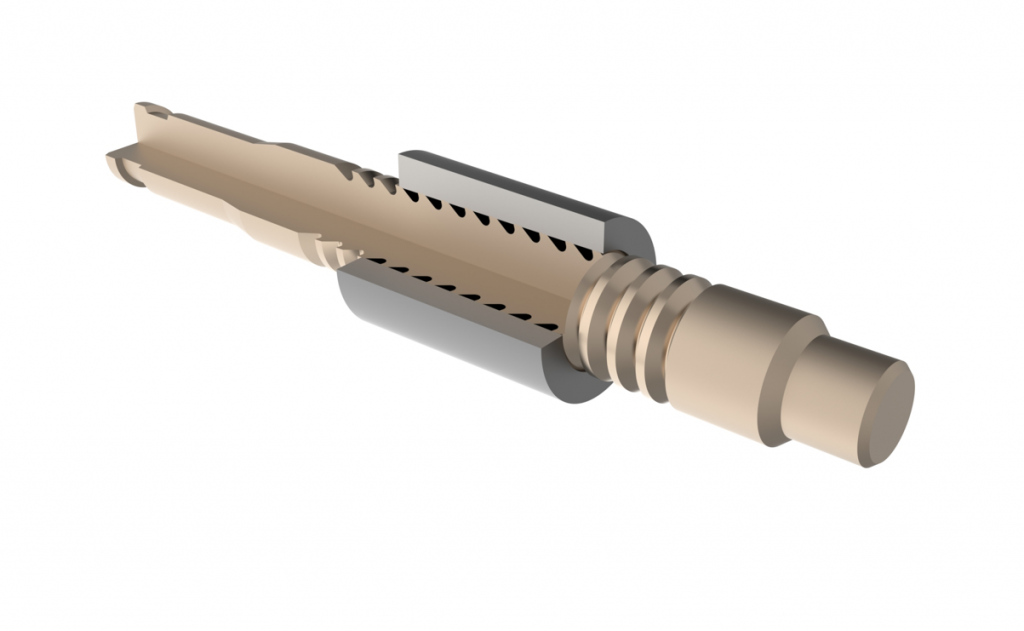
Esempio di una broccia a compressione
Il punto in cui viene applicata la forza di avanzamento all’utensile si ripercuote inevitabilmente sulla geometria dell’utensile stesso. Una broccia a compressione, infatti, sarà di lunghezza inferiore di quella a trazione poiché più è lunga la broccia più si rischia di avere instabilità e deformazioni da compressione (buckling).
UTENSILI A INSERTI
Gli utensili ad inserti sono di più recente invenzione. Infatti, i primi utensili di questo tipo iniziarono a comparire in ambito industriale solamente a partire dagli anni ’60. Gli utensili che sono maggiormente impiegati in ambito industriale sono:
- Frese da contornatura
- Frese da spianatura
- Frese da profilatura e copiatura
- Frese da scanalatura e troncatura
- Frese ad alto avanzamento
- Punta a forare
FRESE DA CONTORNATURA
Una fresa da contornatura è una fresa che è capace di creare un piano e simultaneamente lavorare uno spallamento. Il concetto di base è lo stesso delle frese a candela piatte in quanto si stanno lavorando due superfici perpendicolari tra di loro.
Data la lavorazione di contornatura, infatti, è possibile selezionare un utensile che abbia un tagliente più o meno lungo e che abbia un diametro adeguato dipendentemente alle features da lavorare.
- La lavorazione di spallamenti poco profondi è possibile utilizzare frese con un diametro maggiore allo spessore dello spallamento per ottenere un impegno radiale relativo minimo e poter compiere la lavorazione in una sola passata e garantire comunque un’ottima precisione sulla perpendicolarità delle facce createsi.
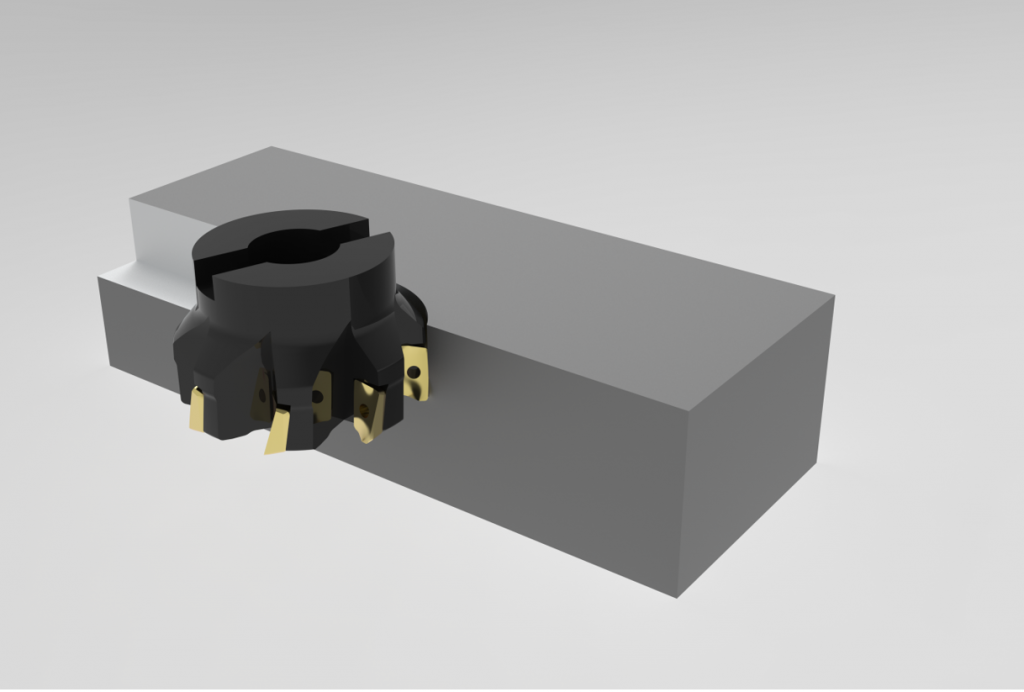
Esempio di una fresa da contornatura
- Nella lavorazione di uno spallamento profondo la geometria della fresa è caratterizzata da un tagliente verticale più lungo.
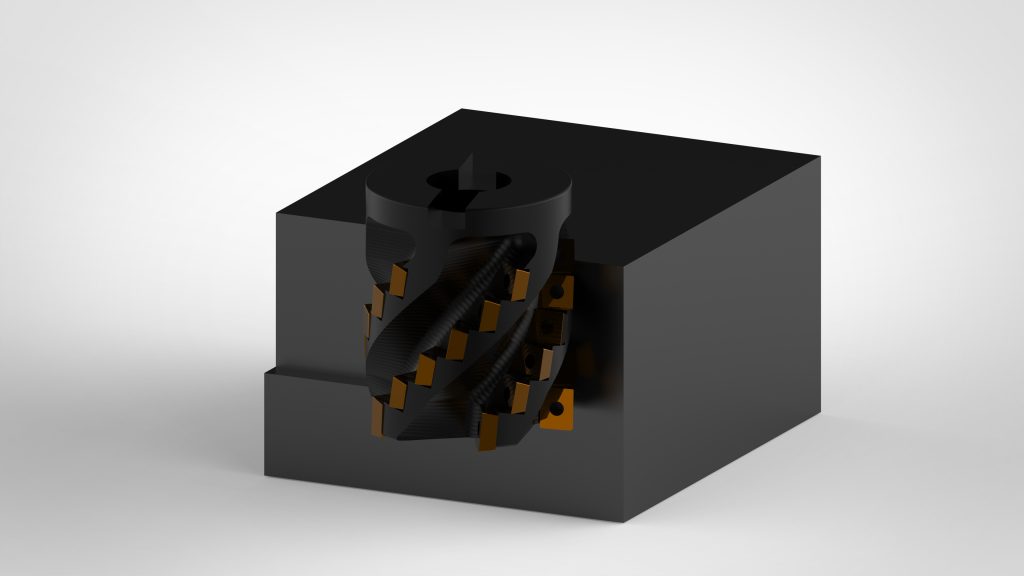
Esempio di una fresa da contornatura per alti spallamenti (fresa a riccio)
- Per spallamenti caratterizzati dal piano orizzontale molto ampio e uno spessore relativamente basso è possibile optare per una fresa a disco che permette di avere una profondità di taglio radiale ampia con lo svantaggio di accedere solo a profondità di taglio assiali limitate.
FRESA DA SPIANATURA
Una fresa da spianatura è un utensile in grado di ricavare una superfice lavorata planare in direzione perpendicolare all’asse di rotazione. Questo tipo di frese è tra le più utilizzate nell’ambito della manifattura pesante. Dato l’ampio l’utilizzo col tempo la geometria di questo utensile si è diversificato adattandosi alle più disparate necessità di processo. In generale l’applicativo delle frese da spianatura si può suddividere in tre subcategorie ovvero:
- Spianatura generale (caratterizzate da geometrie che permettono sia sgrossatura che finitura)
- Alti avanzamenti (caratterizzate da geometrie del tagliente che permettono velocità di avanzamento elevate e di conseguenza MRR elevati)
- Finitura (con inserti raschianti)
Uno dei principali aspetti che caratterizza una fresa da spianatura è l’angolo di registrazione del tagliente. Infatti è il fattore che più influenza le direzioni delle forze di taglio impattando sulla stabilità della lavorazione.
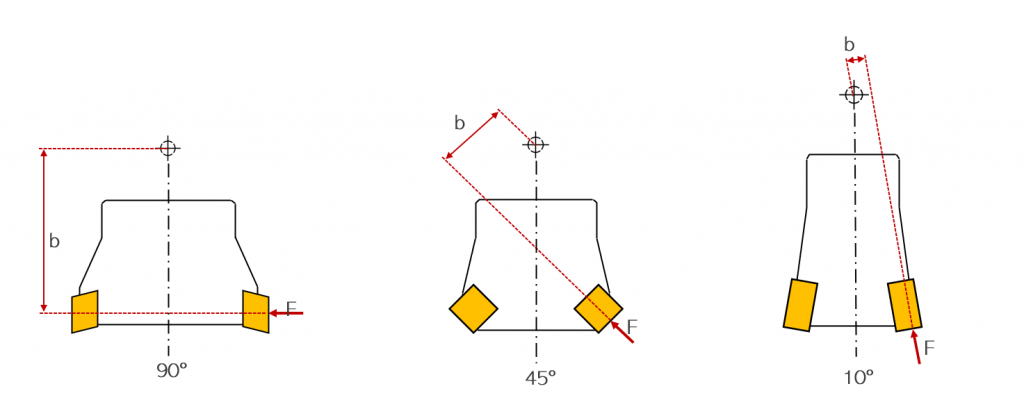
Schema di frese da spianatura con angolo di registrazione decrescente
In generale un basso angolo di registrazione permette una lavorazione molto più stabile rispetto ad altre configurazioni. La forza radiale in questo caso è quasi nulla minimizzando la flessione dell’utensile. Per questa ragione, la fresa può essere lunga come nel caso di una fresatura del fondo di una tasca profonda. Lo svantaggio principale è invece la profondità di passata ridotta.
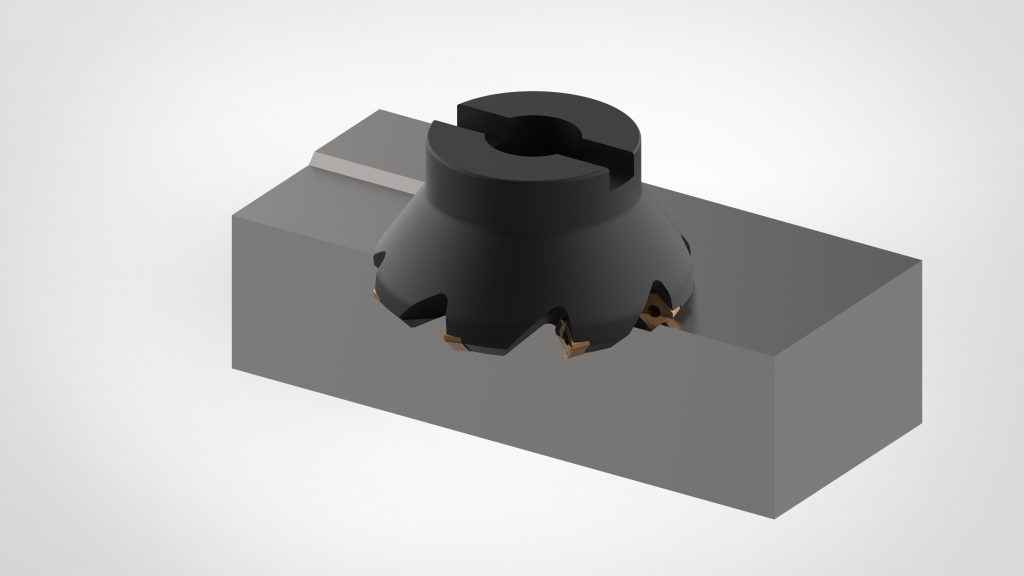
Esempio di una fresa da spianatura con angolo di registrazione intermedio
Al contrario una fresa con un angolo di registrazione di 90° presenta una minore stabilità in termini di dinamica del taglio in quanto le forze generate sono scaricate radialmente e dunque inficiano sulla stabilità. Il vantaggio maggiore di questo uensile è la sua versatilità, poiché permette affondamenti assiali maggiori e di poter essere impiegata anche per altre operazioni come la contornatura.
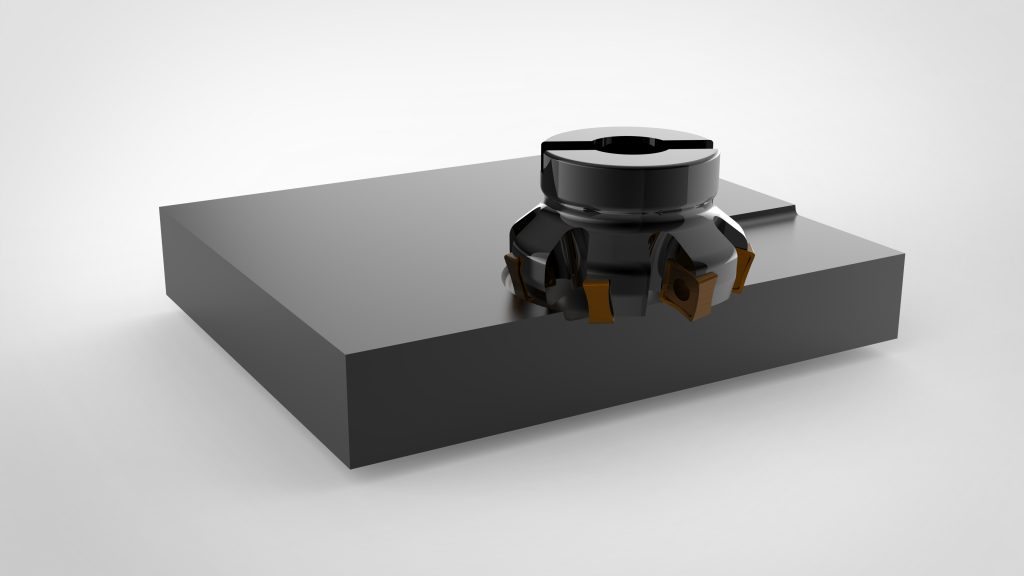
Esempio di una fresa da spianatura con alto angolo di registrazione
Oltre ad inserti di geometria prismatica esisono inserti con geometria rotonda o con raggiature molto accentuate. L’adozione di questa geometria aiuta ad ottenere un tagliente più robusto e anche uno spessore di truciolo variabile in funzione della profondità di passata assiale. Mantenendo, infatti, un affondamento ridotto rispetto al raggio dell’inserto lo spessore di truciolo rimane basso nonstante un avanzamento alto mentre mantenendo un affondamento paragonabile al raggio gli avanzamenti sostenibili sono inferiori poichè lo spessore di truciolo aumenta.
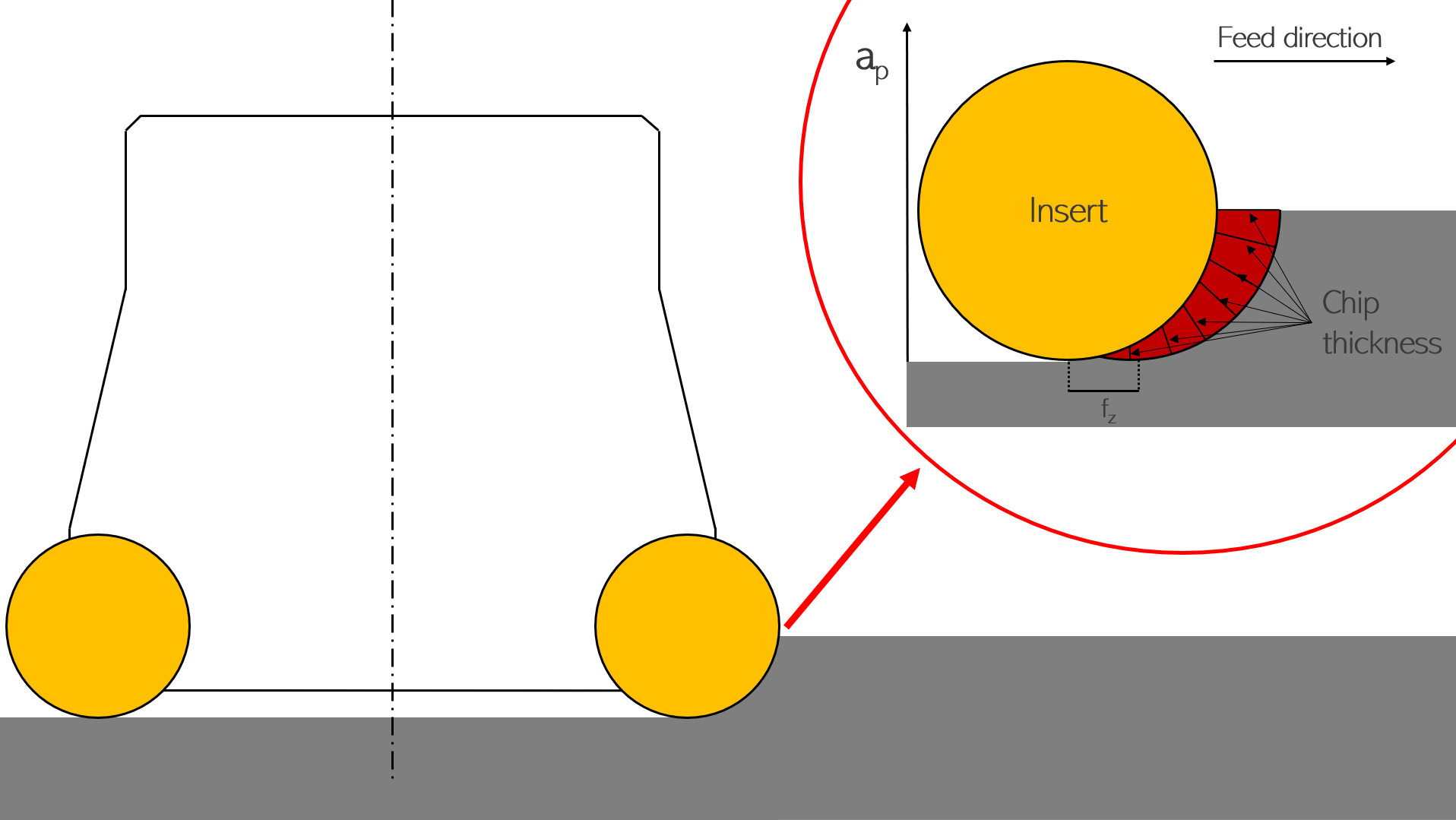
Schema di una fresa da spianatura con inserti circolari che mostra l’aumentare dello spessore di truciolo all’aumentare dell’impegno assiale
Nei processi di finitura infine viene privilegiato l’utilizzo di fresa ad inserti raschianti. Questa geometria è caratterizzata da 2 taglienti, uno primario con angolo di registrazione che va da 25° a 90° e uno secondario con angolo di registrazione di 0°, ovvero parallelo alla superficie lavorata. La funzione del secondo tagliente è di evitare la formazione delle creste che si formano sulla superficie di un componente fresato dovuto al passaggio dell’inserto.
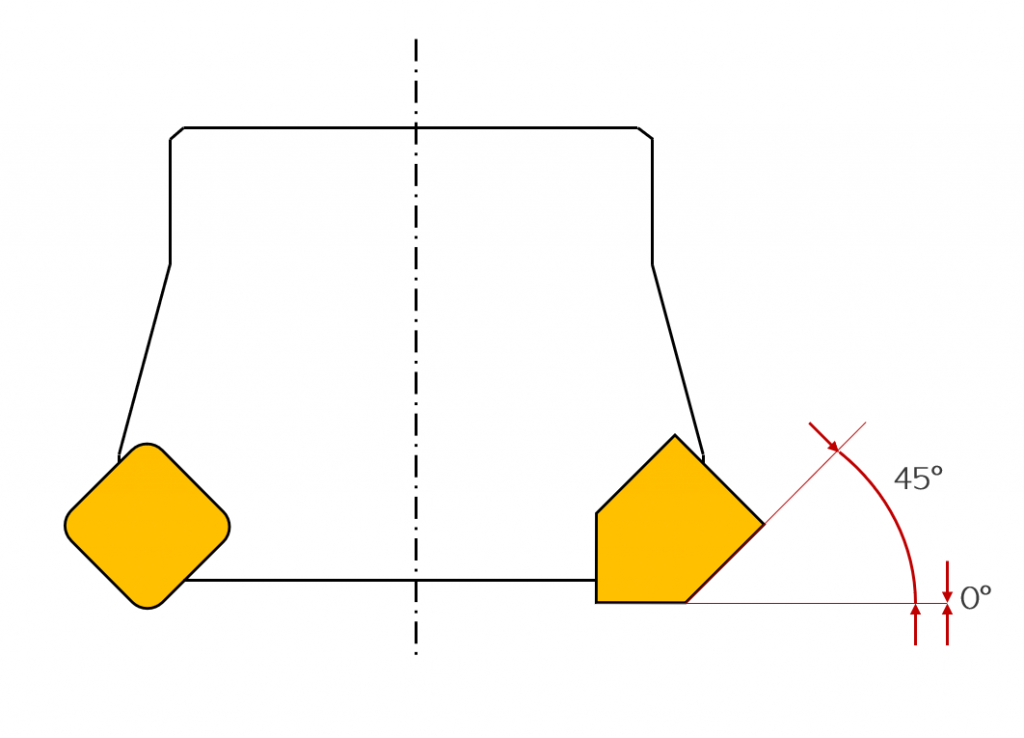
Esempio di un inserto raschiante con i due taglienti rispettivamente a 0° e 45°
FRESE DA PROFILATURA E COPIATURA
Una fresa da profilatura è una fresa capace di lavorare geometrie concave e convesse con asse inclinato. Per questo tipo di geometrie prive di spigoli vivi o raggi/raccordi di piccole dimensioni, il processo di lavorazione si divide in tre step principali:
- Sgrossatura
- Semifinitura
- Finitura
In questo tipo di operazioni la fresa a inserti da profilatura si colloca nella maggior parte dei casi nelle operazioni di sgrossatura e semifinitura mentre per quelle di finitura, più spesso si usano frese integrali a testa sferica.
Le frese a inserti concepite per la profilatura e la copiatura sono caratterizzate da inserti rotondi o raggiati ampi. Il motivo per cui viene selezionata questa tipologia di utensili per le prime due fasi lavorazione è che il tasso di rimozione del materiale è elevato e dunque è necessario soddisfare requisiti di stabilità e di avanzamenti al dente notevoli.
Le due principali geometrie adottate per le operazioni di profilatura e copiatura sono di due tipologie:
- Ad inserti rotondi, dove la forma del corpo utensile è simile a quello da spianatura/contornatura, ma gli inserti applicati sono circolari. Questa geometria è spesso ottimizzata per le fasi di sgrossatura in quanto la forma dell’inserto rotondo permette di avere un tagliente più robusto e di distribuire meglio le pressioni di taglio.
- A testa sferica, dove la geometria è più esile. In questo caso, il diametro della fresa riesce ad essere più contenuto grazie alla forma oblunga degli inserti. Questa configurazione viene preferita in fase di sgrossatura/semifinitura.
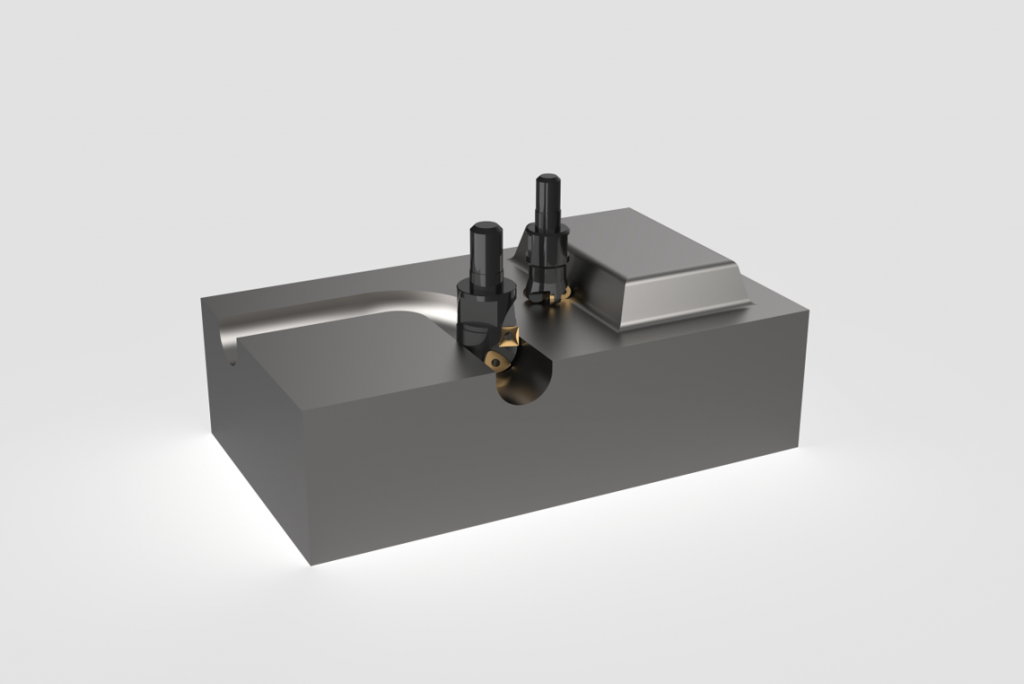
Esempio di frese da profilatura a inserti sagomati e rotondi
FRESE DA SCANALATURA E TRONCATURA
Una fresa da scanalatura è una fresa capace di rimuovere materiale da pieno e generare solchi all’interno del materiale di varie dimensioni e rapporti di forma (tra la larghezza e altezza del solco stesso). Per questo genere di operazioni si scelgono principalmente 2 tipi di frese: a disco e a candela. Le frese a disco possono essere utilizzate anche come utensili da troncatura.
- Le frese a disco sono frese dal rapporto tra ingombro radiale e assiale elevato. La sua forma e il principio di lavorazione ricorda molto quella della sega circolare. Gli inserti sono montati alle estremità radiali del disco. Questa geometria permette di ricavare scanalature larghe quanto l’ingombro assiale degli inserti. Grazie all’elevato diametro dell’utensile non è necessario avere al mandrino regimi di rotazione elevati in quanto la velocità di taglio è garantita dal diametro della fresa. Questo tipo di utensili possono essere utilizzati per troncare sezioni e realizzare scanalature rettilinee aperte (che partono dall’esterno del pezzo).
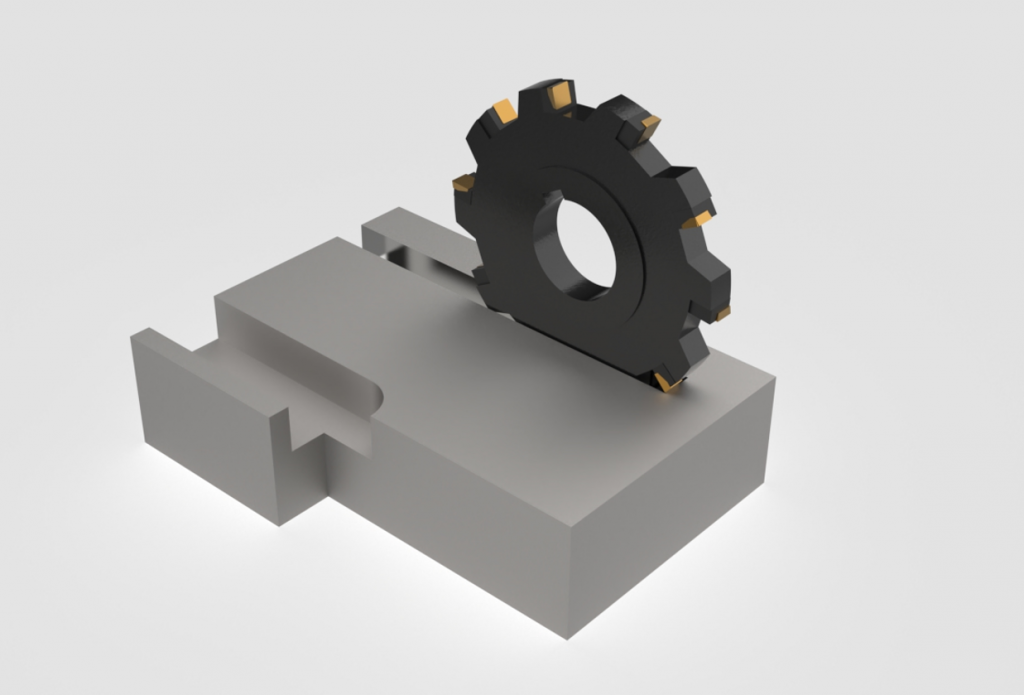
Esempio di una fresa a disco ad inserti
I più grossi limiti introdotti sono la linearità obbligata delle scanalature e la difficile evacuazione del truciolo. Al netto degli svantaggi però questa configurazione permette di avere un’elevata stabilità nella lavorazione, alta produttività e di realizzare scanalature a larghezze differenti in quanto si possono usare inserti di spessore differente a parità di fresa.
- La fresa a candela si presenta come una classica fresa da fresatura frontale con taglienti sia sulla testa che sul lato. Sono frese capaci di rimuovere materiale sia in direzione assiale che radiale. Le frese utilizzate hanno la geometria adatta anche a lavorazioni di spianatura e contornatura (con i limiti di diametri di taglio del caso).
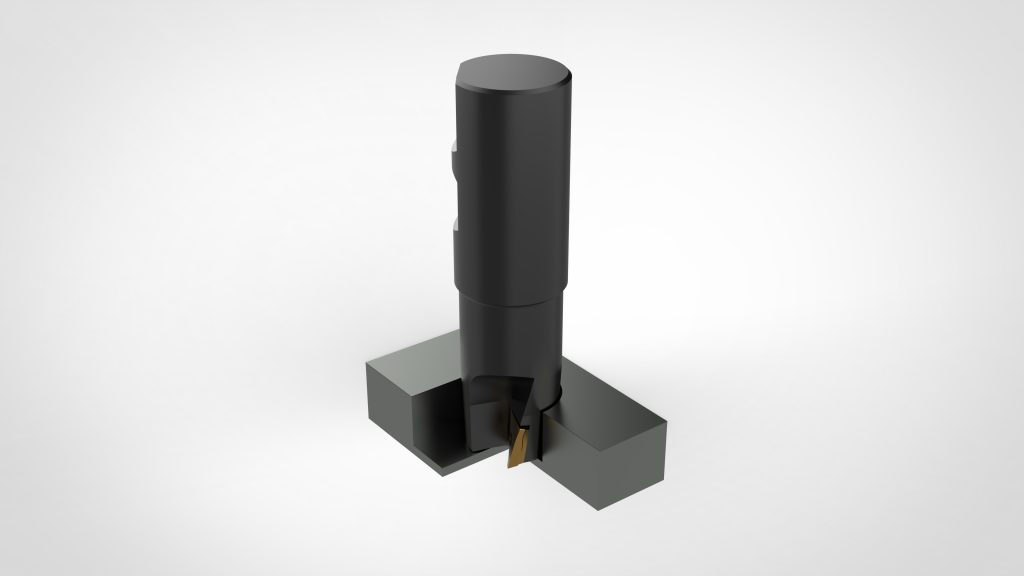
Esempio di una fresa da scanalatura a candela
I principali vantaggi dati dall’adozione di questo utensile sono la possibilità di effettuare scanalature rette, curve o anche angolate e la possibilità di realizzare cave chiuse (ingresso a tuffo o in materiale preforato). I principali svantaggi invece sono le elevate forze generate, il limite sulla profondità raggiungibile e la maggior suscettibilità alle vibrazioni (meno stabilità nella lavorazione).
FRESE AD ALTO AVANZAMENTO
La fresatura ad alto avanzamento corrisponde intrinsecamente ad un’operazione ad elevata produttività. Questo tipo di utensile è stato concepito per raggiungere valori di MMR (Material Removal Rate) elevati. Queste frese in generale possono essere sia integrali che a inserti ma queste ultime sono quelle che permettono di lavorare a regimi più estremi. Le condizioni di lavoro di questi utensili corrispondono a un’elevata velocità di avanzamento accoppiata ad una ridotta profondità di taglio. Questi parametri permettono di avere una sezione di truciolo ottimizzata in quanto, riducendo la profondità di taglio e aumentando l’avanzamento è possibile generale forze di taglio dirette maggiormente verso l’asse Z (verso il mandrino) piuttosto che in direzione radiale, direzione assai più problematica per l’utensile. Adottando questa strategia si assicurano una maggiore stabilità del processo e un conseguente prolungamento della vita dell’utensile.
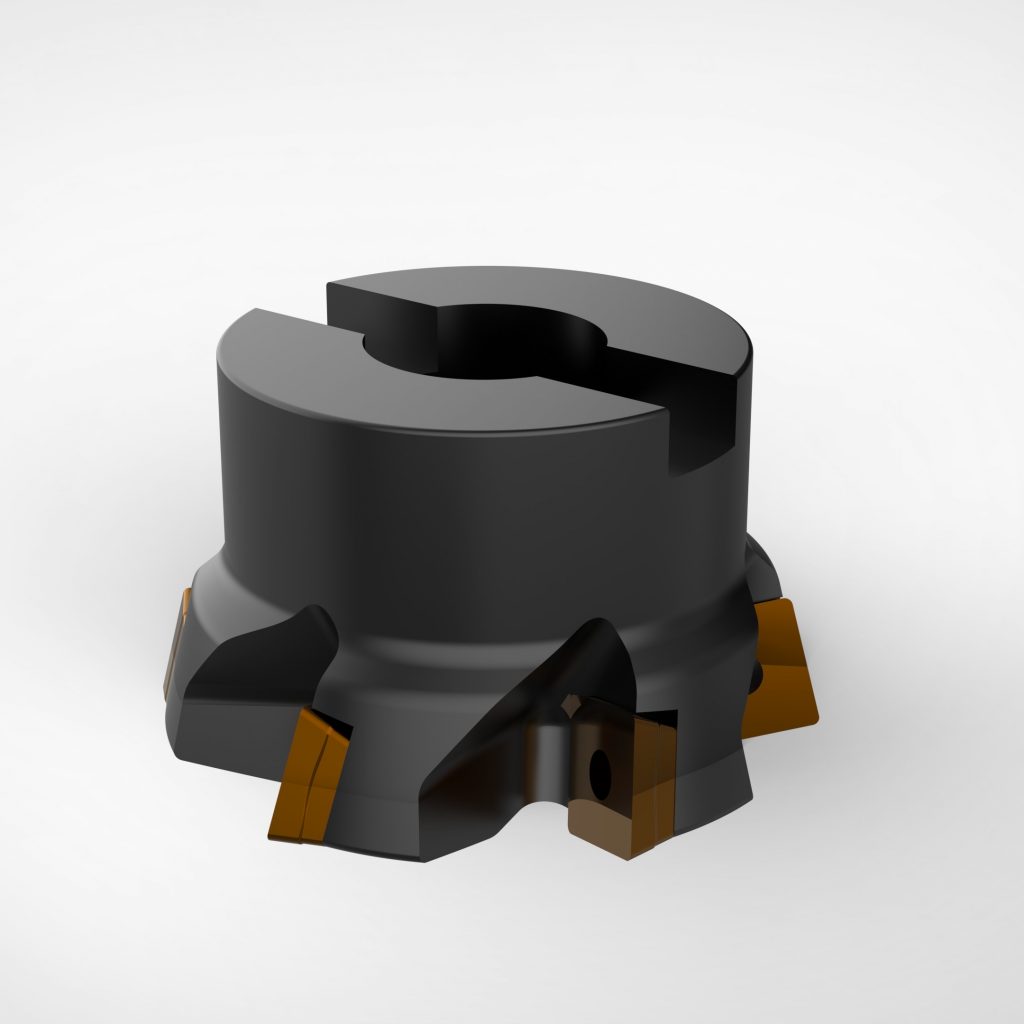
Esempio di una fresa ad alto avanzamento
L’applicazione di questo concetto può essere fatta su molteplici tipologie di fresa ma principalmente sulle frese da spianatura. La morfologia può variare parecchio soprattutto in base al materiale e alle dimensioni. Ad esempio il numero di taglienti può variare da 4 a 14. Il motivo di avere così tanti denti su una singola fresa è che permette di avere un elevato avanzamento al giro e di avere più denti in presa anche a impegni radiali bassi. Questa configurazione si mostra molto efficace quando bisogna spianare grandi superifici e rimuovere molto materiale. A parità di esborso iniziale (dovuto alla quantità di inserti necessari per l’attrezzaggio) si ha un guadagno di produttività (alto MRR) e il consumo degli inserti decrementa.
PUNTA A FORARE AD INSERTI
Le punte a forare ad inserti hanno la medesima funzione di quelle integrali ma, se messe a confronto, presentano diversi vantaggi.
Per quanto concerne la struttura generale dell’utensile ciò che è più importante è la sua capacità di creare condizioni di lavoro meno affette da vibrazioni e fenomeni di chatter. Ciò comporta naturalmente una lavorazione più precisa e con finitura superficiale migliore. Anche in questo caso la lubrorefrigerazione è importante ed avere un corpo in materiale più facilmente lavorabile che nella maggior parte dei casi è acciaio, aiuta ad ottenere canali interni di apporto liquidi più efficienti e avere un’irrorazione della zona di taglio migliore, permettendo un tasso di rimozione materiale ancora maggiore.
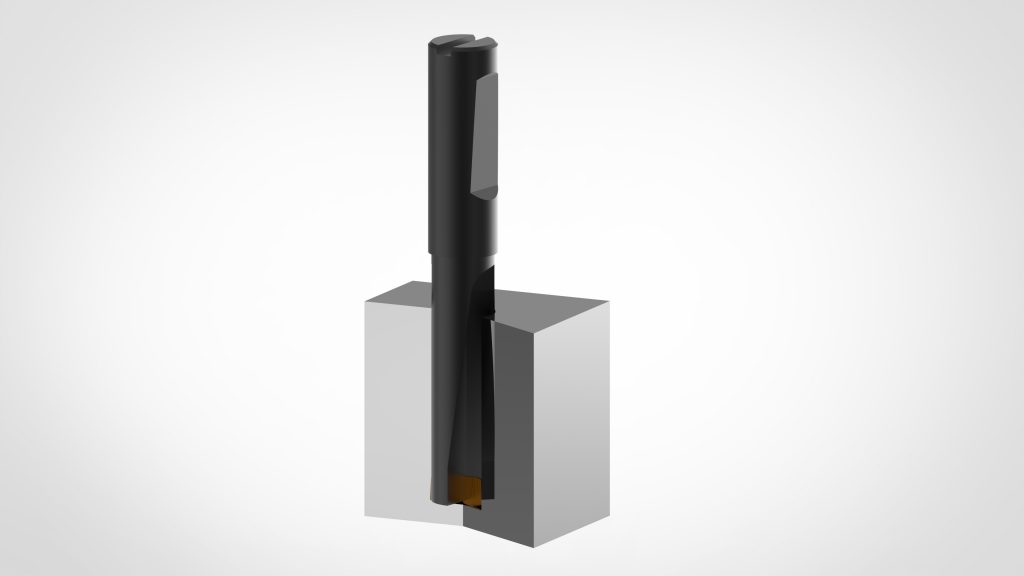
Esempio di una punta a forare a inserti
I vantaggi di cui godono le punte a forare ad inserti sono principalmente due:
- Consentono innanzitutto, come per le frese, di raggiungere dimensioni superiori a quelle integrali sia per il costrutto più economico che per le limitazioni strutturali presentate da un corpo interamente in metallo duro ma hanno a loro volta un limite minimo di dimensioni.
- Richiedono un primo esborso più oneroso rispetto ad una punta integrale ma a lungo andare il costo iniziale viene ammortizzato poichè ad essere rimpiazzato sono solo gli inserti usurati e non l’intero utensile.
- COMPETENZE ACQUISITE
Hai conseguito le seguenti competenze:
- Imparare a conoscere le principali tipologie di utensili
- Imparare a selezionare la tipologia corretta di utensile in base all’applicazione
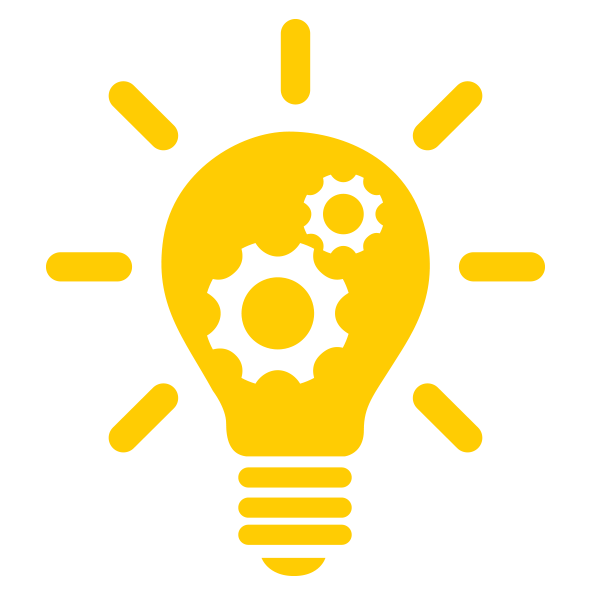
CONTATTI UTILI, LINK E DOWNLOAD
Contatti
- Per gli studenti:
Prof. Annoni Massimiliano, Politecnico di Milano: massimiliano.annoni@polimi.it - Per gli educatori:
Prof. Annoni Massimiliano, Politecnico di Milano: massimiliano.annoni@polimi.it - Per le imprese:
Prof. Annoni Massimiliano, Politecnico di Milano: massimiliano.annoni@polimi.it