I centri di lavorazione
PREREQUISITI
- Conoscenza base dei processi per asportazione di truciolo
- Conoscenza base dei concetti generali dei processi meccanici
- TEMPO DI APPRENDIMENTO: 45 min.
OBIETTIVI
- Capire le principali funzioni degli organi che compongono una macchina CNC
- Capire le principali tipologie di macchine CNC
- Principali caratteristiche cinematiche
- Principali componenti lavorati
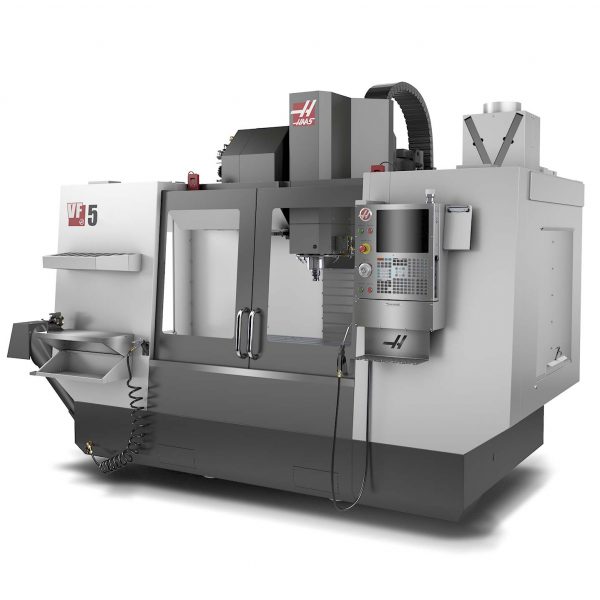
Fresatrice verticale Haas VF-5/40TR
INTRODUZIONE
Un centro di lavoro è una macchina utensile controllata da computer utilizzata per eseguire un’ampia varietà di operazioni e processi di lavorazione. Questi centri sono sempre più diffusi nel mondo manifatturiero. Questa diffusione è dovuta alla possibilità di incrementare in maniera sostanziale le performance produttive dovute all’automazione del processo produttivo che incrementa la sua precisione e la ripetibilità.
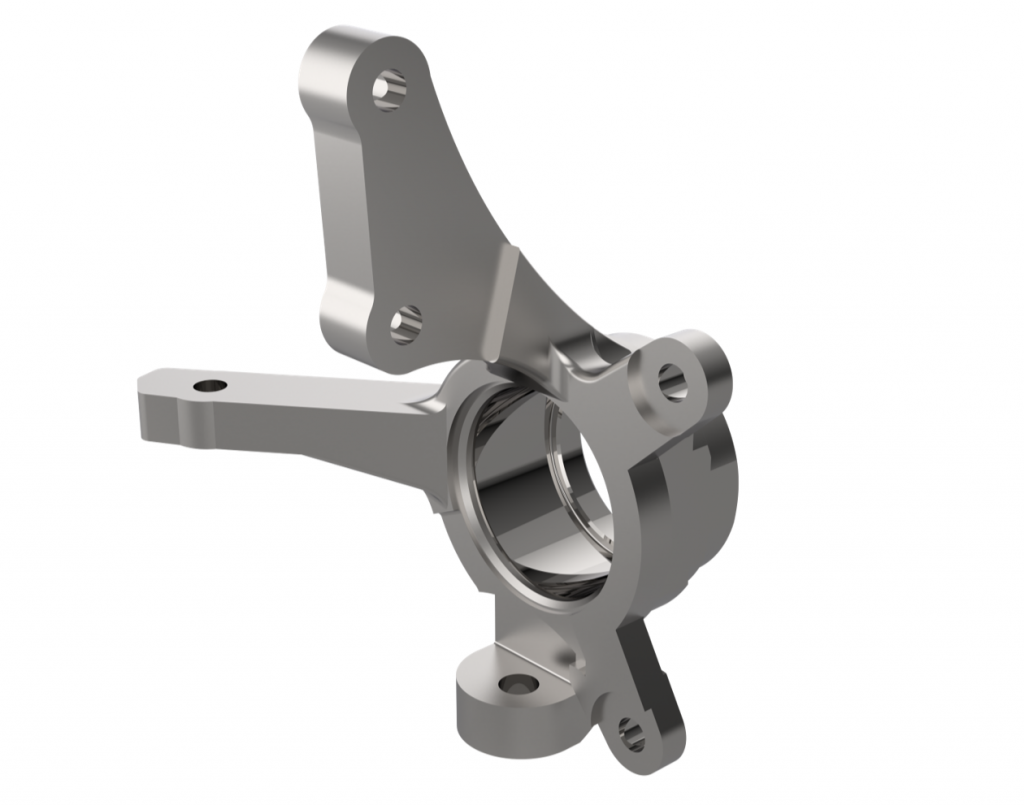
Esempio di un componente lavorato per fresatura (grabcad.com)
COS'È UN CENTRO DI LAVORAZIONE
Un centro di lavorazione è una macchina utensile dotata di controllo numerico in grado di eseguire autonomamente in modo ripetibile e preciso una vasta gamma di operazioni descritte in un programma in linguaggio standard (ISO 6983-1:2009) chiamato G-code, che solitamente viene ampliato con comandi specifici del produttore del controllo e della macchina utensile stessa. Ciò che contraddistingue un centro di lavorazione da una semplice macchina utensile è anche la versatilità nelle lavorazioni eseguibili. É infatti possibile eseguire un’ampia gamma di operazioni (fresatura, foratura, tornitura, lappatura, rettifica etc…) senza la necessità di manipolare il componente e doverlo trasferire da una macchina utensile all’altra quando si cambia tipologia di lavorazione.
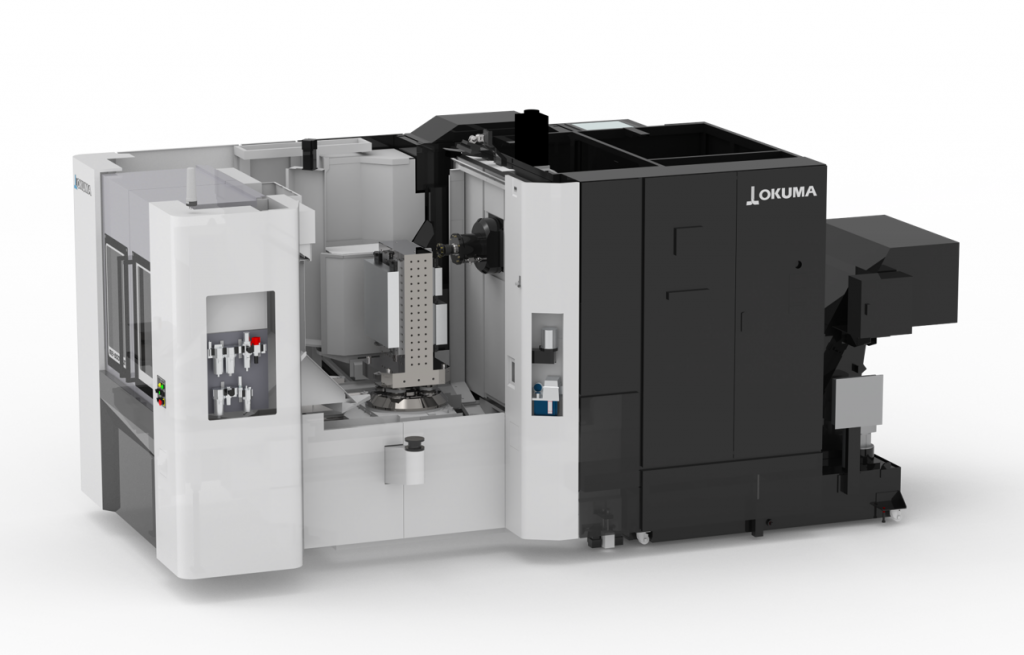
Okuma MB-5000HII è un centro di fresatura con mandrino orizzontale
ANATOMIA GENERALE DI UN CENTRO DI LAVORAZIONE
L’anatomia di un centro di lavorazione può essere molto complessa ma ci sono elementi in comune a tutti i macchinari che sono necessari ai fini dell’operatività.
IL BASAMENTO O CHASSIS
Il primo componente che viene introdotto è lo chassis della macchina. Questo componente è spesso trascurato ma racchiude in sé molte caratteristiche che collaborano al buon funzionamento della macchina utensile. Esso, infatti, deve:
- Svolgere la funzione strutturale di sostegno statico ai componenti della macchina. In secondo luogo, deve garantire una rigidezza tale da assicurare deformazioni minime che possono scaturire dalle inerzie dei componenti mobili e dalle forze di taglio durante le lavorazioni.
- Un’altra funzione importante che svolge lo chassis è quella di smorzare il più possibile le vibrazioni provenienti sia dall’ambiente di lavoro circostante sia dal macchinario stesso (vibrazioni prodotte da altre macchine, motori elettrici ed altri azionamenti sia interni alla macchina che esterni).
- Ridurre le deformazioni termiche dovute al calore generato dalla lavorazione e dagli azionamenti, ma anche dall’ambiente circostante.
Minimizzare deformazioni e vibrazioni ha un’enorme importanza pratica in quanto esse possono essere la causa di difetti nel componente prodotto come tolleranze non rispettate o finiture superficiali fuori specifica.
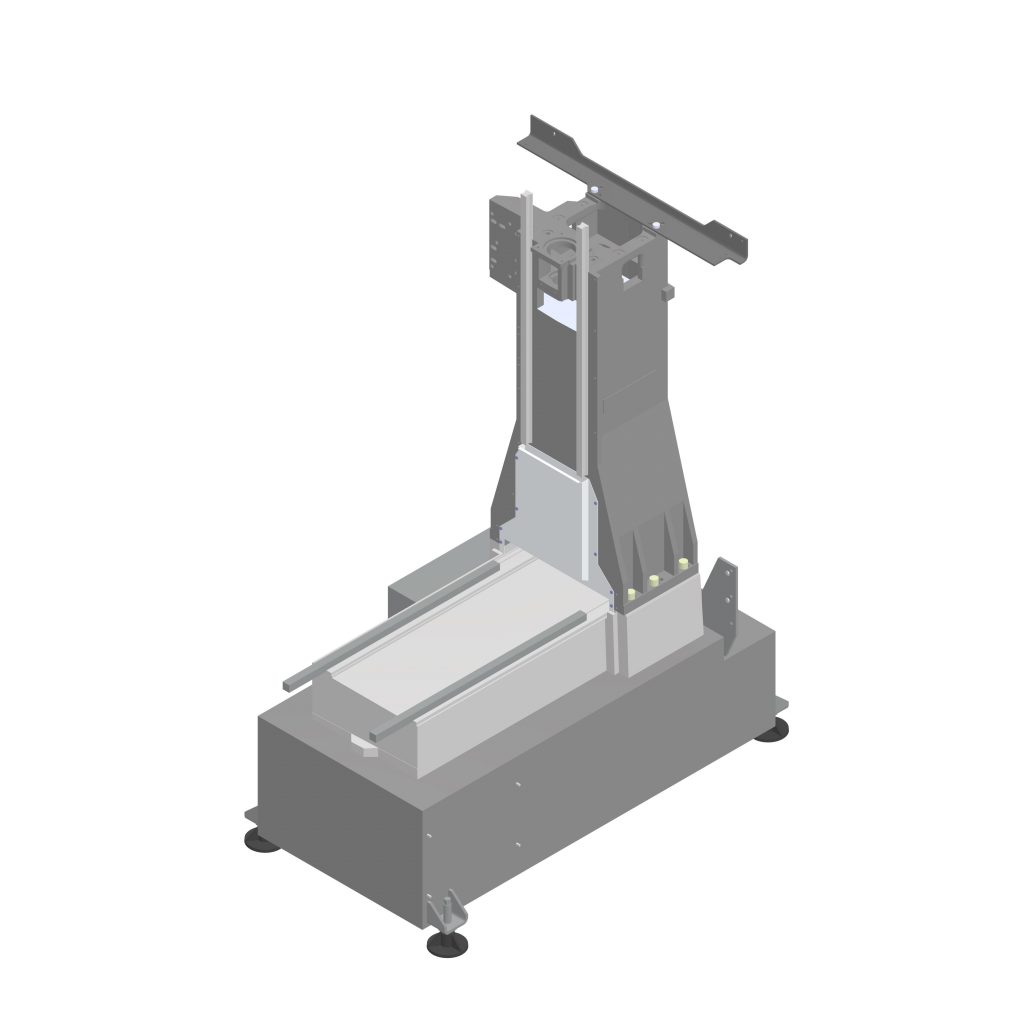
Esempio di chassis di un centro di lavorazione
GLI ASSI
Gli assi della macchina si occupano del movimento motorizzato roto-traslatorio (ovvero traslazione e rotazione) relativo tra utensile e grezzo.
Gli assi lineari:
Gli assi che si occupano del moto traslatorio (ovvero lungo X, Y, Z) sono formati a loro volta da diversi componenti:
- le guide lineari
- la tavola (o blocco mobile) su cui è montato il mandrino o il grezzo
- il motore (non presente in figura)
- la vite di comando (non presente in figura), ovvero l’organo adibito alla trasmissione del moto tra motore e blocco mobile
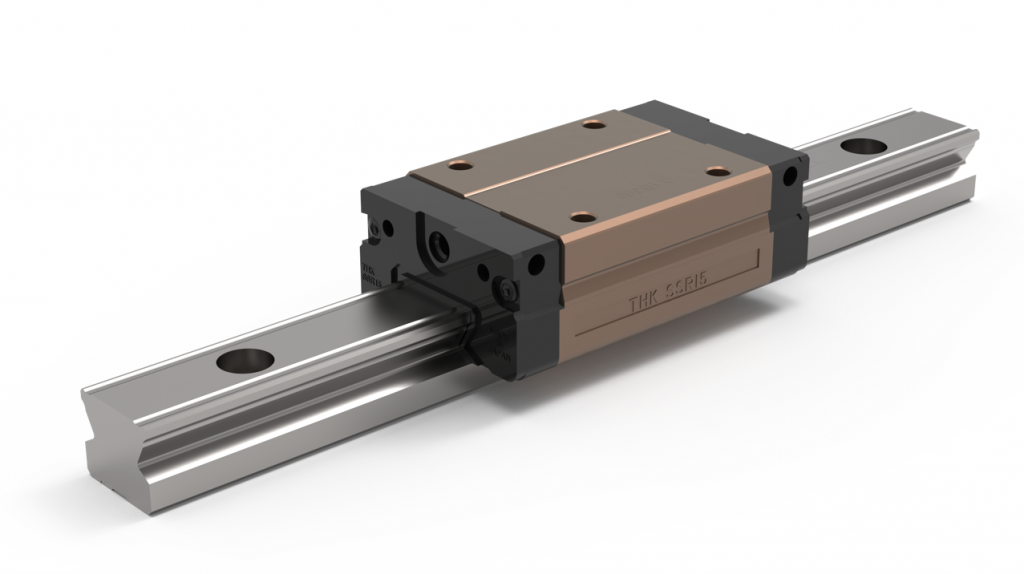
Esempio di una guida lineare con blocco mobile di una fresatrice
Alcune delle macchine più precise sono dotate di motori lineari che non hanno la necessità di convertire un movimento rotatorio in uno lineare. Essi però sono costosi e necessitano di controlli e sistemi di smaltimento del calore adeguati. Attualmente hanno una implementazione limitata (ad esempio la YASDA YMC650+RT20).
Come per lo chassis, anche le guide e i blocchi mobili devono essere concepiti in modo tale da poter reggere i carichi scaturiti dal processo riducendo le deflessioni. In questo caso sono necessarie elevate rigidezze flessionali e torsionali per garantire la precisione nel movimento e nel posizionamento degli organi.
Gli assi rotatori:
Questi sono gli assi che implementano il moto rotatorio sono concepiti in modo differente in quanto la rotazione viene conferita direttamente dal motore elettrico senza organi che convertano il tipo di moto. Eventualmente può essere interposto un riduttore o una trassione per regolare la coppia ed il regime di rotazione (e.g. un sistema cinghia-puleggia).
IL MANDRINO
Il mandrino rappresenta il cuore pulsante del centro di lavorazione in quanto ad esso è affidato il compito di fornire la potenza e trasmetterla all’utensile per asportare materiale. Ci sono diverse tipologie di mandrino ma quelle più diffuse sono due:
- Il mandrino azionato a cinghia, in cui il motore non è coassiale all’asse di rotazione dell’utensile
- Il mandrino con motore integrato, in cui la disposizione dei componenti è coassiale
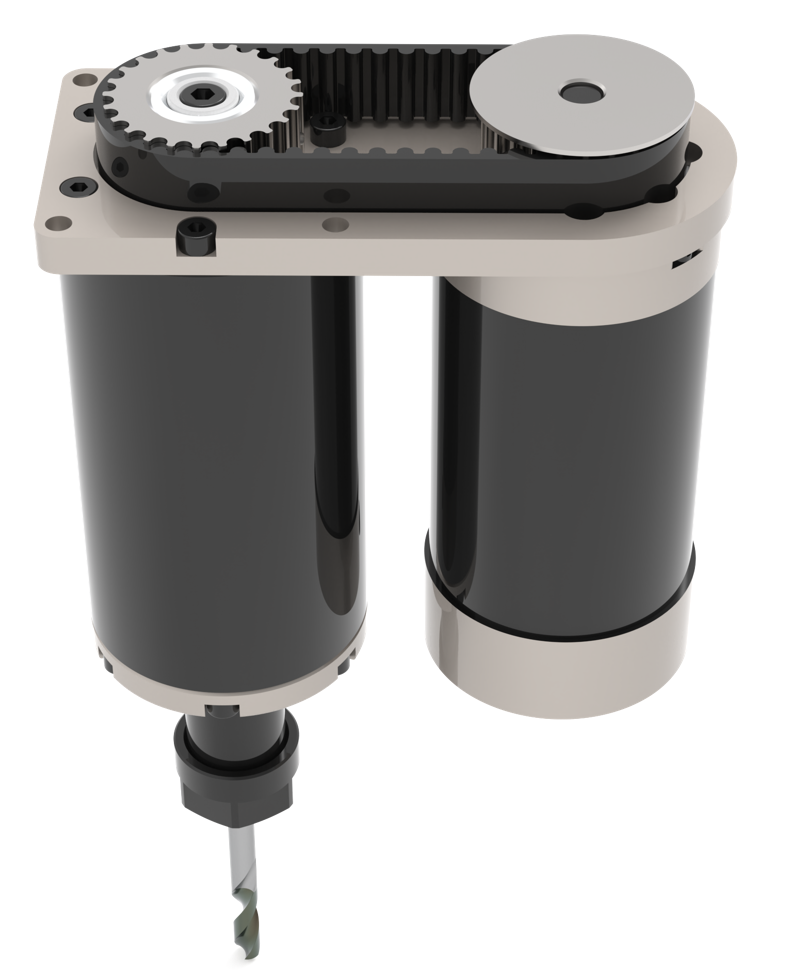
Mandrino con azionamento a cinghia
La prima tipologia introdotta è quella con azionamento a cinghia. Questo tipo di architettura presenta diversi vantaggi:
- essendo il motore separato dall’asse mandrino, vi è la possibilità di montare un motore di grosse dimensioni, dunque, di accedere ad elevate potenze e coppie
- è un’architettura economica in quanto i componenti sono di semplice fattura
- vi è inoltre la possibilità di montare un riduttore a più velocità, rendendo la macchina più versatile in termini di regime di rotazione e coppia disponibile
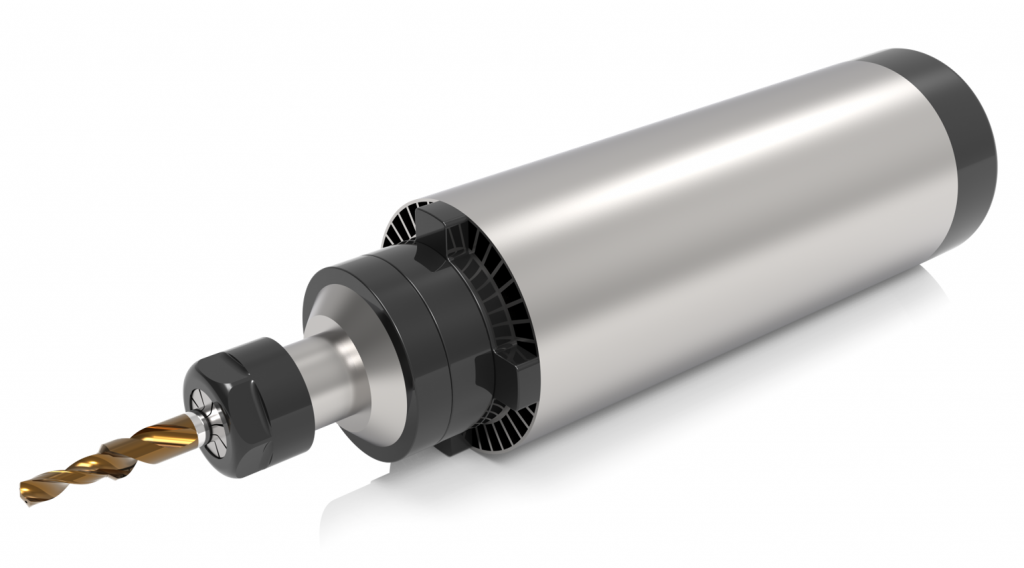
Mandrino con motore integrato
La seconda tipologia di mandrino ha un motore integrato. Questo tipo di architettura permette una connessione diretta tra motore e asse mandrino rimuovendo la necessità di cinghie e cuscinetti che resistano ad elevati carichi radiali. Vengono introdotte però altre limitazioni quali la necessità di un motore dal diametro contenuto e di conseguenza bassa coppia e sulla potenza espresse al mandrino dovuti allo spazio disponibile. Il vantaggio maggiore apportato da questa configurazione è la possibilità di raggiungere regimi di rotazione elevati senza imporre carichi elevati ai componenti meccanici.
Per quanto riguarda il motore impiegato per azionare i mandrini il più comune è il motore trifase AC a induzione. Il rotore è calettato all’albero del mandrino nel caso della soluzione integrata o alla puleggia nel caso a cinghia. Gli aspetti importanti che caratterizzano il motore di un mandrino sono le curve di coppia /regime di rotazione e potenza/regime di rotazione. Come in un classico motore elettrico, la coppia massima viene raggiunta a bassissimi regimi e questa diminuisce man mano che il regime di rotazione aumenta. Per questo motivo è importante tenere in considerazione la disponibilità di coppia e potenza in fase di progettazione della lavorazione per poter individuare la regione ottimale di parametri di taglio da utilizzare quali velocità di taglio, avanzamento e profondità di passata.
IL PORTAUTENSILI
Il mandrino da solo non è sufficiente per compiere una lavorazione ma servono un utensile e un’interfaccia che lo possa vincolare al mandrino. Per questo si utilizzano i cosiddetti portautensili, che permetteono l’accoppiamento del mandrino con l’utensile che offra rigidezza, precisione di centraggio e trasmissione della coppia. A tal fine esistono diverse tipologie di interfaccia mandrino/portautensile come, ad esempio, HSK (ISO 12164-1, DIN 69893), BT (JIS B 6339-2, MAS 403) etc.
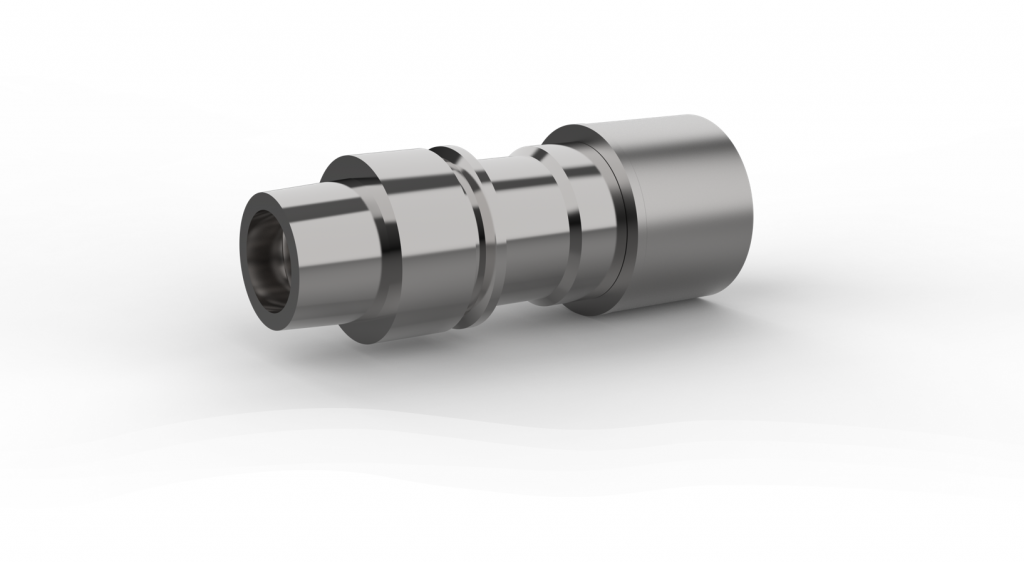
Portautensile con interfaccia HSK (Portautensili BIG KAISER HSK E32 MEGA13N 70)
MAGAZZINO UTENSILI
Si passa ora a presentare una delle parti più innovative introdotte dai centri di lavorazione CNC, ovvero il magazzino utensili con sistema ATC (Automatic Tool Change). Il magazzino di queste macchine può essere realizzato in molteplici architetture e dimensioni. Si pensi che la capienza di un magazzino utensili può variare da poche unità fino a varie centinaia. É importante sottolineare come il sistema ATC permetta la sostituzione automatizzata dell’utensile sul mandrino in modo preciso e veloce.
Si distinguono principalmente tre tipi di magazzino ATC: a tamburo, a catena o a scaffale robotizzato.
- Il primo ha la forma di un tamburo rotante con gli utensili disposti attorno alla sua circonferenza
- Il secondo invece comprende sistemi a catena e ruote dentate con gli utensili sempre disposti in posizione o orizzontale o verticale
- Il terzo infine comprende sistemi scaffalati dotati di un meccanismo automatizzato in grado di prelevare l’utensile dalla rastrelliera e portarlo al mandrino
Automatizzando tale step si assicura un guadagno non indifferente di performance in quanto il cambio viene effettuato in pochissimi secondi e garantisce un livello di sicurezza maggiore per l’operatore e per l’utensile stesso in quanto il primo non deve avvicinarsi al macchinario e il secondo invece viene maneggiato molto meno.
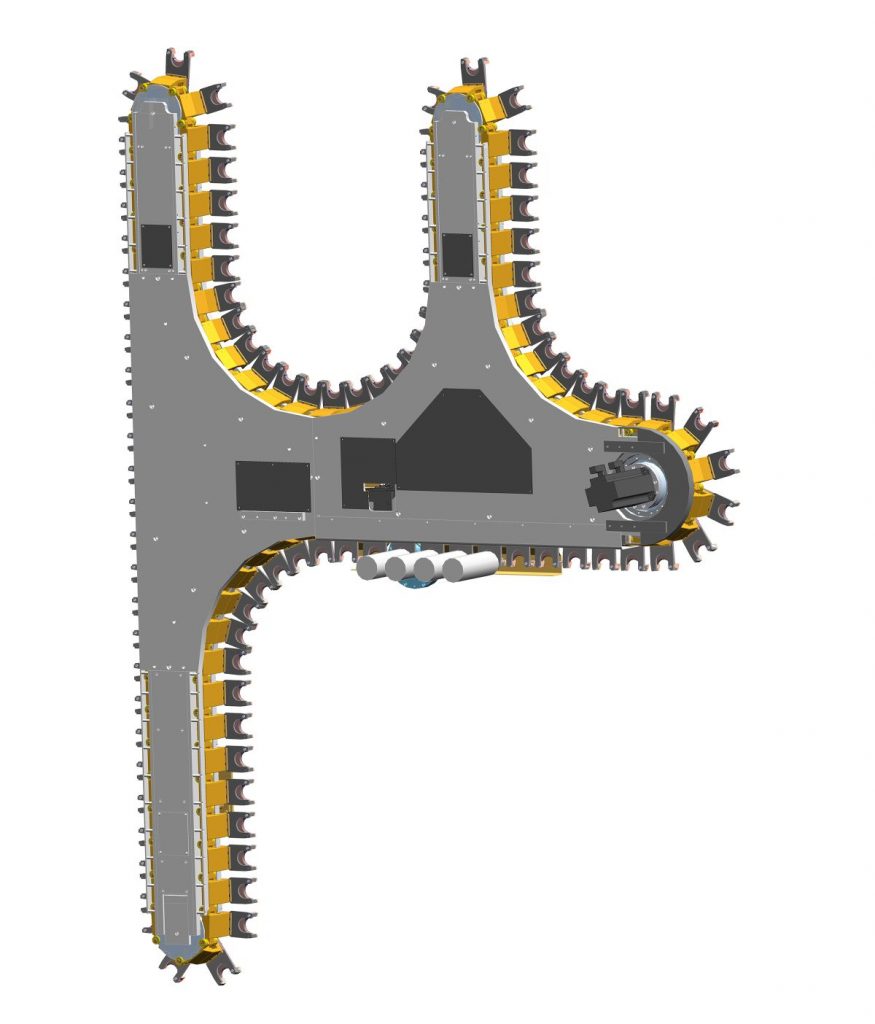
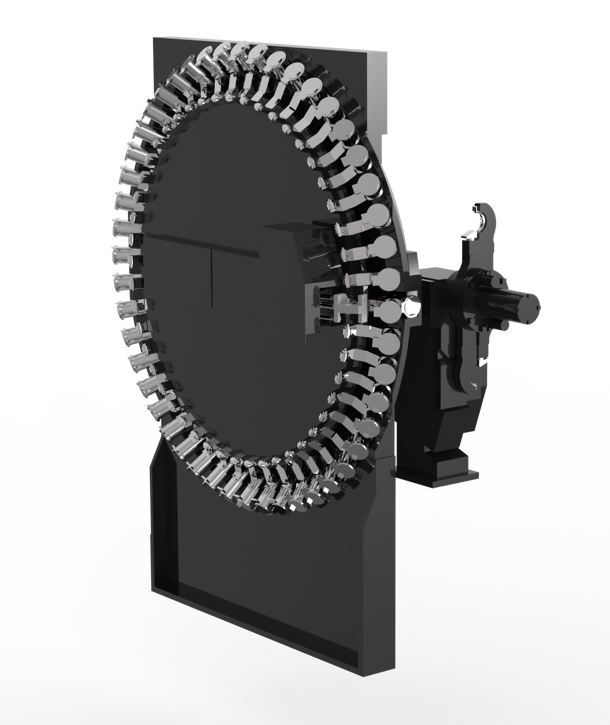
Esempi di ATC a catena (e.g. OKUMA GENOS M460V-5AX)e a tamburo (e.g. HAAS UMC 750 SS)
Ora che gli organi meccanici generali della macchina sono stati brevemente presentati si introduce il tipo di controllo che permette al centro di lavorazione di agire automaticamente.
COME FUNZIONA IL CONTROLLO DEI CENTRI DI LAVORAZIONE?
Il controllo di una macchina CNC (Computer Numerical Control) è composto da tre unità: l’unità NC che offre l’interfaccia utente ed esegue il controllo della posizione, l’unità motore e l’unità driver. In senso stretto, solo l’unità NC è chiamata sistema CNC. Da un punto di vista funzionale, il sistema CNC è costituito dall’unità HMI o MMI (Human/Man Machine Interface), dall’unità NCK (Numerical Control Kernel) e dall’unità PLC (Programmable Logic Control).
L’unità HMI offre l’interfaccia tra NC e utente, esegue il comando di funzionamento della macchina, visualizza lo stato della macchina e offre funzioni per la modifica del programma pezzo.
L’unità NCK, essendo il nucleo del sistema CNC, interpreta il programma ed esegue l’interpolazione, il controllo della posizione, la compensazione degli errori in base al programma interpretato, controlla il sistema servo e determina la lavorazione del pezzo.
Il PLC controlla in sequenza il cambio utensile, la velocità del mandrino, il cambio pezzo, l’elaborazione del segnale in/out e svolge il ruolo di controllo del comportamento della macchina, ad eccezione del controllo servo.
L'HMI
L’unità HMI offre l’interfaccia (pulsanti, sirene, cicalini, schermi e interruttori) necessaria all’utente per comunicare con la macchine utensili e viceversa. Esistono molti tipi di interfaccia utente basati sui concetti di progettazione del produttore CNC. Le funzioni dell’interfaccia utente sono generalmente classificate in cinque gruppi:
- Funzioni operative: queste funzioni sono quelle utilizzate più frequentemente e supportano il funzionamento della macchina. Parte di queste funzioni sono svolte dal display che mostra lo stato della macchina. Ad esempio vengono mostrati la posizione, la distanza da percorrere e l’avanzamento, la velocità del mandrino, il blocco in esecuzione ecc…
- Funzioni di impostazione dei parametri: il funzionamento di un sistema CNC è caratterizzato da parametri che vanno a condizionare il suo comportamento, essi sono classificati in tre tipi: parametri macchina (utilizzati per impostare la regolazione della macchina, il sistema di azionamento servo/mandrino, l’offset utensile, le coordinate di lavoro e il limite delle corse degli assi), parametri di programma (devono essere impostati durante la modifica del programma pezzo, ad esempio gli offset dell’origine macchine) e parametri di personalizzazione (vengono utilizzati per adattare la macchina alle esigenze dell’utente, ad esempio colori, lingua ecc…)
- Funzioni di modifica del programma: queste funzioni sono in grado di modificare il programma pezzo, che è un codice G basato sullo standard EIA/ISO. In pratica, è necessario che l’utente conosca i codici G/M ed esegua calcoli matematici per modificare il programma in codice G. Poiché il calcolo matematico rende difficile modificare i programmi, sulle macchine più moderne sono stati introdotti sistemi di programmazione conversazionale, ovvero un software che permette l’inserimento di operazioni parametriche pre-programmate.
- Funzioni di monitoraggio e allarme: il sistema CNC informa l’utente dello stato della macchina ed esegue le attività programmate e informa l’utente del risultato. Queste funzioni sono essenziali quando le macchine utensili vengono eseguite ad alta velocità. Svolgono il ruolo di fornire informazioni di monitoraggio come lo stato di allarme, il metodo di ripristino di emergenza, lo stato del PLC e il diagramma ladder in esecuzione.
- Funzioni di servizio/utilità: sono fornite molte funzioni utili per assistere gli utenti. La funzione DNC per la trasmissione del programma pezzo, che viene modificato esternamente al CNC, il servizio file per la copia dei parametri interni e comunicazione per la connessione con i computer.
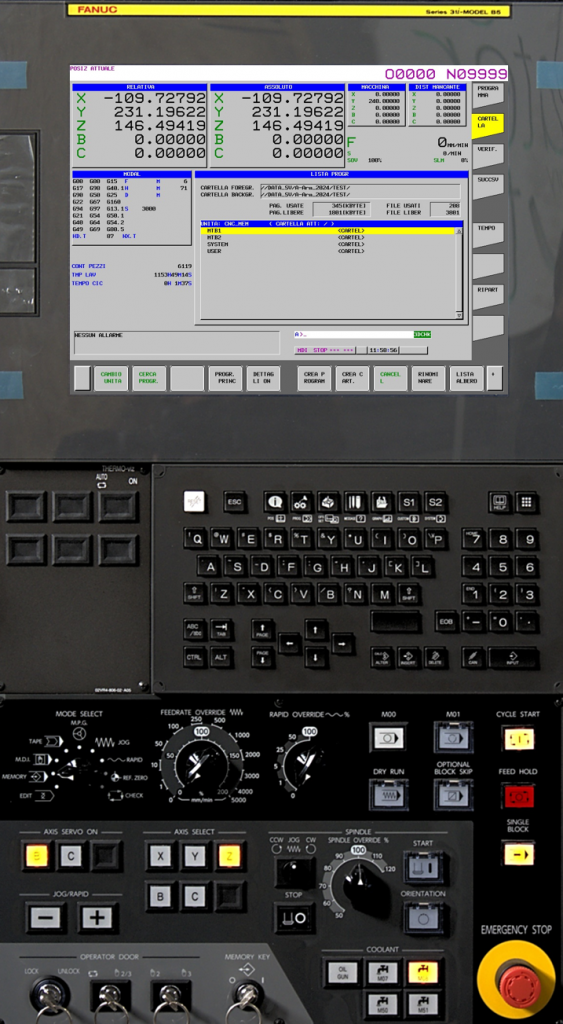
HMI della YASDA YMC650+RT20
L'NCK
Le funzioni principali dell’unità NCK sono: interpretare i programmi ISO, calcolare l’interpolazione degli assi, fungere da controller di accelerazione/decelerazione e da controller di posizione.
- L’interprete svolge il ruolo di leggere un programma. La sua lettura avviene in blocchi ASCII e vengono memorizzati i dati interpretati nella memoria interna per l’interpolatore. In generale, l’NC emette gli ordini relativi ai dati interpretati e l’interprete legge e interpreta il blocco successivo mentre il comando viene eseguito. In alcuni casi la velocità con cui vengono eseguiti i comandi è superiore a quella con cui vengono letti creando potenzialmente dei fermi tra un comando e l’altro. Per evitare questi arresti momentanei durante l’esecuzione di un programma letti i blocchi successivi a quello in esecuzione e i comandi processati vengono salvati momentaneamente in un buffer nell’attesa di esser eseguiti (internal data buffer).
- L’interpolatore svolge il ruolo di leggere in sequenza i dati dell’internal data buffer, calcolare la posizione e la velocità per unità di tempo di ciascun asse e memorizzare il risultato in un buffer FIFO per il controller di accelerazione/decelerazione. In un sistema a controllo numerico possono essere utlizzati quattro tipi di interpolatore differenti: lineare, circolare, parabolico ed spline. A seconda dell’applicazinoe della macchina viene impiegata la tipologia più adatta. L’interpolatore genera un impulso corrispondente ai dati del percorso in base al tipo di traiettoria e invia l’impulso al buffer FIFO. Il numero di impulsi è deciso in base alla lunghezza del percorso e la frequenza degli impulsi è basata sulla velocità.
- Se il controllo della posizione venisse eseguito utilizzando i dati generati dall’interpolatore, si verificano grandi vibrazioni meccaniche e urti ogni volta che il movimento degli azionamenti inizia e si arresta all’esecuzione di ogni singolo avanzamento comandato. Per prevenire vibrazioni meccaniche e urti, il filtro per il controllo di accelerazione/decelerazione viene eseguito prima che i dati interpolati vengano inviati al controller di posizione. Questo metodo è chiamato metodo “acceleration/deceleration after-interpolation“. Esiste anche un metodo “acceleration/deceleration-before-interpolation“, in cui il controllo di accelerazione/decelerazione viene eseguito prima dell’interpolazione.
- I dati, dal controller di accelerazione/decelerazione, vengono inviati a un controller di posizione ed questo viene eseguito in base ai dati trasmessi in un intervallo di tempo costante. Un controllo della posizione in genere significa un controller PID (Proportional Integral Derivative) e invia comandi di velocità al sistema di azionamento del motore per ridurre al minimo la differenza di posizione tra la posizione comandata e la posizione effettiva rilevata dall’encoder.
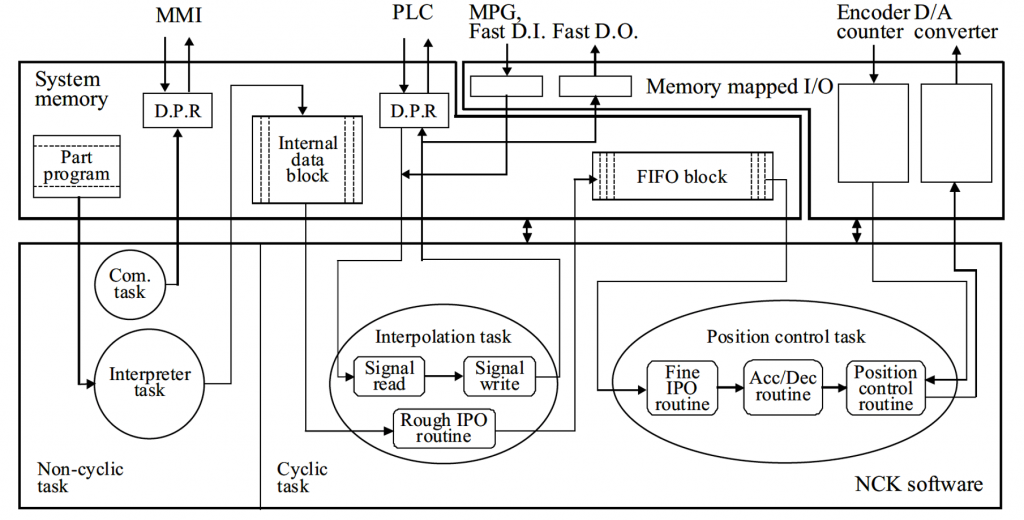
Schema logico dell’unità NGK (“Theory and design of CNC systems”, Suh, S.H., Kang, S.K., Chung, D.H. and Stroud, I., 2008. )
IL PLC
Il PLC viene utilizzato per eseguire il controllo sequenziale di azioni in una macchina CNC. In passato, il controllo logico veniva eseguito utilizzando hardware costituito da relè, contatori, timer e circuiti. Pertanto, era considerato un controllore logico basato su hardware.
Tuttavia, i recenti sistemi PLC sono costituiti da alcuni dispositivi elettrici tra cui microprocessori e memoria, in grado di eseguire operazioni logiche, la funzione contatore, la funzione timer e operazioni aritmetiche. Pertanto, un sistema PLC può essere definito come un controllore logico basato su software. I vantaggi dei sistemi PLC basati su software sono i seguenti:
- Flessibilità: la logica di controllo può essere modificata modificando solo un programma.
- Scalabilità: l’espansione di un sistema è possibile aggiungendo moduli e modificando i programmi.
- Efficienza economica: la riduzione dei costi è possibile grazie alla riduzione dei tempi di progettazione, all’elevata affidabilità e alla facile manutenzione.
- Miniaturizzazione: le dimensioni di installazione sono inferiori rispetto a una scatola di controllo relè.
- Affidabilità: la probabilità di guasti dovuti a un contatto difettoso diminuisce grazie all’utilizzo di un semiconduttore.
- Prestazioni: sono possibili funzioni avanzate come operazioni aritmetiche e modifica dei dati.
L’architettura hardware dell’unità PLC di un sistema NC comprende un microprocessore, una memoria di sistema, una memoria di programma e un modulo di input/output. Non appena l’alimentazione viene attivata, la memoria di sistema imposta l’ambiente hardware del PLC e la memoria di programma, gestisce input/output, relè/timer/contatore e memorizza un programma utente e i dati da interpretare dal microprocessore.
L’unità PLC di un sistema CNC è simile ad un sistema generico PLC, ma è presente un controller ausiliario che assiste in parte delle funzioni dell’unità NCK. Esistono cinque differenti linguaggi di programmazione standardizzati di PLC (IEC 1131-3):
- Ladder Diagrams (LD)
- Function Block Diagram (FBD)
- Sequential Function Chart (SFC)
- Structured Text (ST o STX)
- Instruction List (IL)
Quello più diffuso dei cinque è l’LD grazie alla sua concezione grafica intuitiva.
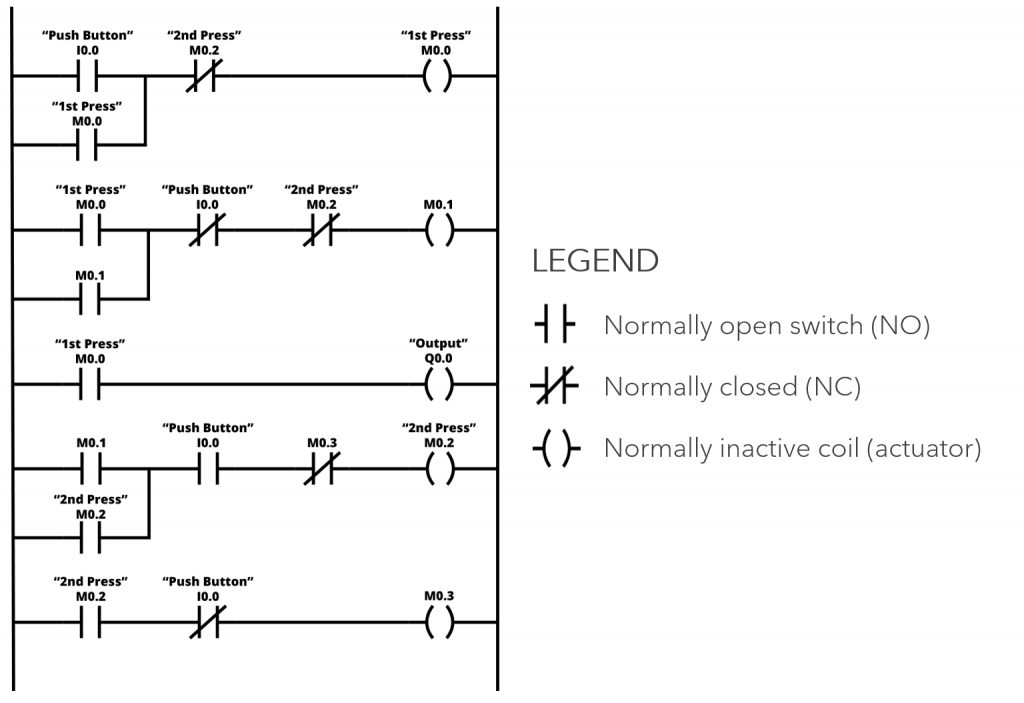
Esempio di programmazione in linguaggio Ladder Logic
CLASSIFICAZIONE IN BASE ALLA TECNOLOGIA DI LAVORAZIONE E ALLA POSIZIONE DEGLI ASSI
La principale caratteristica a cui ci si riferisce per classificare un centro di lavorazione è il numero di gradi di libertà disponibili per la lavorazione ovvero il numero di assi azionabili dalla macchina. Le tipologie più comuni di centri di lavorazione sono le seguenti:
- 2 assi lineari, in cui gli assi interpolati sono solo 2
- 2 assi e mezzo lineari, in cui gli assi interpolati sono 2 mentre il terzo è movimentato solo in posizionamento
- 3 assi lineari, in cui gli assi interpolati sono tutti e 3 (X, Y e Z)
- 4 assi, in cui gli assi movimentati sono 3 di traslazione e uno di rotazione
- 5 assi, in cui gli assi interpolati sono 3 di traslazione e 2 di rotazione garantendo una quasi completa libertà di movimento nello spazio rimanendo entro i limiti geometrici e di mobilità degli assi della macchina (fine corsa, ingombro dell’attrezzatura e del grezzo). Il sesto asse è di rotazione lungo l’asse dell’utensile.
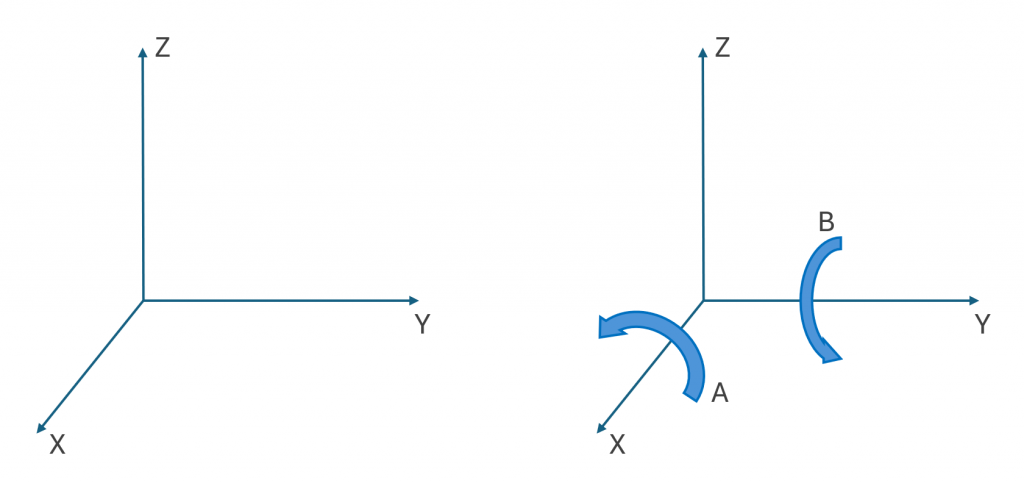
Gradi di libertà di una macchina a 3 e 5 assi
Esistono centri di lavorazione che presentano più di 5 assi di lavorazione. Con questo si intende la possibilità di eseguire un movimento tramite assi ridondanti oppure più lavorazioni in parallelo come nel caso delle macchine multi-mandrino (es. INDEX CNC-Mehrspindeldrehautomat MS40-8: Produktiver mit 8 Spindeln! – YouTube).
È possibile fare un’ulteriore distinzione nel vasto panorama rappresentato dai centri di lavorazione. Basandosi sull’applicazione della macchina utensile, i principali tipi di centri di lavorazione sul mercato sono i seguenti:
- Fresatrice Verticale (VMC, Vertical Machining Center) a 3 assi
- Fresatrice Verticale (VMC) a 5 assi
- Fresatrice orizzontale a 4 assi (HMC, Horizontal Machining Center)
- Fresatrice a portale
- Tornio a 2 assi
- Tornio a 3 assi
- Tornio multi-torretta
- Tornio a fantina mobile
FRESATRICE VERTICALE A 3 ASSI
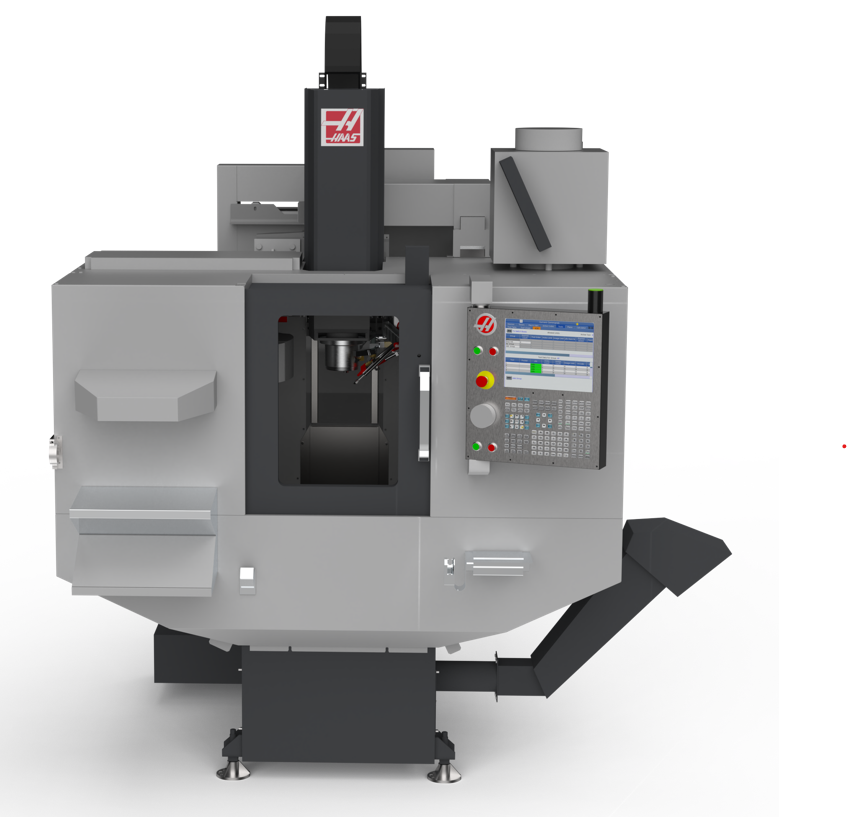
Esempio di una fresatrice verticale a 3 assi (Haas MiniMill)
Una VMC a 3 assi è caratterizzata dalla possibilità di muovere gli assi di traslazione X, Y e Z. È detta verticale in quanto l’asse di rotazione del mandrino è tipicamente in direzione verticale in corrispondenza dell’asse Z. Questi tipi di macchine sono molto diffusi in quanto sono molto versatili, danno la possibilità di realizzare forme di qualsiasi genere, a patto che la geometria del pezzo in lavorazione non abbia sottosquadri. Per concezione hanno un’architettura più economica rispetto ad altre macchine più complesse come quelle a 4 o 5 assi.
La configurazione più generale di una VMC a 3 assi consiste nell’associare la traslazione lungo gli assi X e Y alla tavola di lavorazione su cui è fissato il pezzo mentre quello di traslazione verticale Z all’asse mandrino. Un esempio di questo layout è la Haas MiniMill. Esistono anche altre configurazioni in cui l’asse X o Y o addirittura entrambi sono associati al mandrino.
Applicazione: Realizzazione di componenti da a semplici a complessi senza sottosquadri.
FRESATRICE VERTICALE A 5 ASSI
Una VMC a 5 assi è caratterizzata dalla possibilità di muovere gli assi di traslazione X, Y e Z e contestualmente quelli di rotazione di cui, nella maggior parte dei casi, uno è attorno all’asse X o Y e uno è attorno all’asse Z ma prende alloggio sulla tavola, permettendo al pezzo di girare su sé stesso.
- Asse A → rotazione attorno ad asse X
- Asse B → rotazione attorno ad asse Y
- Asse C → rotazione attorno ad asse Z
Questi centri di lavorazione sono i centri più versatili in assoluto in quando garantiscono il maggior numero gradi di libertà alla lavorazione. Possono lavorare su geometrie complesse e caratterizzate da sottosquadri. Naturalmente tale flessibilità incide sia sul costo del macchinario rendendo questa configurazione una delle più onerose che sulla difficoltà di programmazione.
Una configurazione diffusa di VMC a 5 assi associa un asse traslatorio (X o Y) e due assi rotativi alla tavola di lavorazione, mentre gli altri due assi lineari vengono associati al mandrino. Un esempio di questo layout può essere la Yasda YMC650+RT20. Esistono anche altre configurazioni in cui ad esempio entrambi gli assi X e Y sono responsabili della movimentazione della tavola ecc.
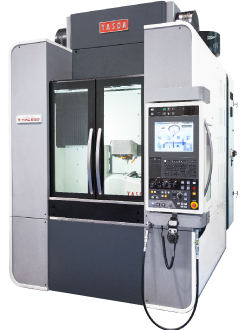
Esempio di una fresatrice verticale a 5 assi (Yasda YMC650+RT20)
È utile sottolineare come la presenza degli assi di rotazione possa concorrere all’efficientamento di un processo realizzabile anche con una fresatrice a 3 assi. La possibilità di variare l’inclinazione tra utensile e pezzo rende possibile l’adozione di strategie efficienti rispetto a quelle che sarebbero implementabili su una macchina a 3 assi. Ciò comporta sia una riduzione dei tempi di produzione sia una maggiore precisione sul pezzo considerando che con una VMC a 5 assi si può il numero di setups anche quando sono previsti più superifici e sottosquadri da lavorare.
Applicazione: Realizzazione di componenti con geometrie molto complesse anche caratterizzate da sottosquadri con la conseguente riduzione del numero di setups.
FRESATRICE ORIZZONTALE A 4 ASSI
Una HMC a 4 assi è caratterizzata dalla possibilità di muovere i 3 assi di traslazione X, Y e Z e contestualmente anche quello di rotazione della tavola. In questo caso la macchina è detta orizzontale perché l’asse di rotazione del mandrino è posto in orizzontale. Secondo la nomenclatura standard l’asse Z è posto in orizzontale coerentemente col mandrino. Un esempio di questo tipo di macchina è la Okuma MB-5000HII.
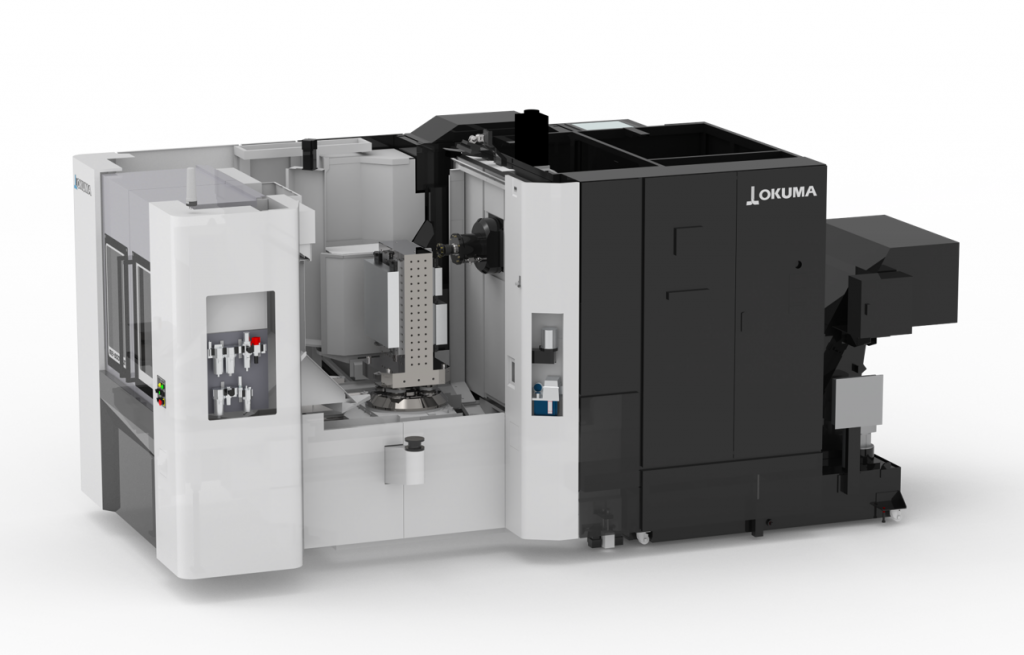
Esempio di una fresatrice orizzontale a 4 assi (Okuma MB-5000HII)
Il vantaggio principale portato da un’architettura di questo genere è la possibilità di lavorare un grezzo di grandi dimensioni bloccandolo sulla tavola oppure grezzi più piccoli bloccandoli in morsa su una apposita attrezzatura (tombstone, v. figura). La posizione del mandrino in orizzontale facilita l’evacuazione del truciolo. Grazie a queste sue peculiarità possono essere montati sulla tavola dei portapezzi detti spalle o squadre (o tombstones) che possono ospitare molti grezzi contemporaneamente e che possono essere lavorati in serie aumentando la produttività della macchina.
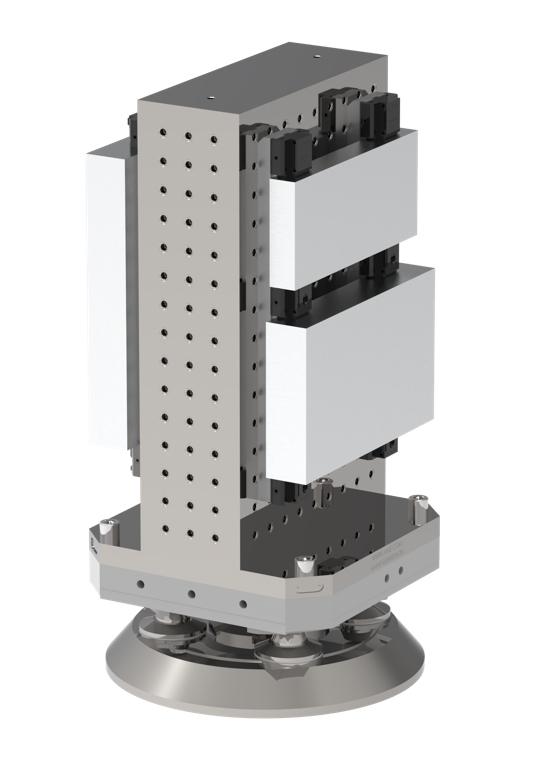
Esempio di una tombstone
Applicazione: Realizzazione di molteplici componenti in serie o in alternativa particolari di grandi dimensioni.
FRESATRICE A PORTALE
La fresatrice a portale è una fresatrice (a tre o a cinque assi) dalla configurazione particolare. Essa infatti è stata concepita principalmente per la realizzazione di componenti di grandi dimensioni per rispondere all’esigenza di avere lunghe corse degli assi. A tal fine questo tipo di fresatrice è composta da due elementi principali che sono il portale ed il letto.
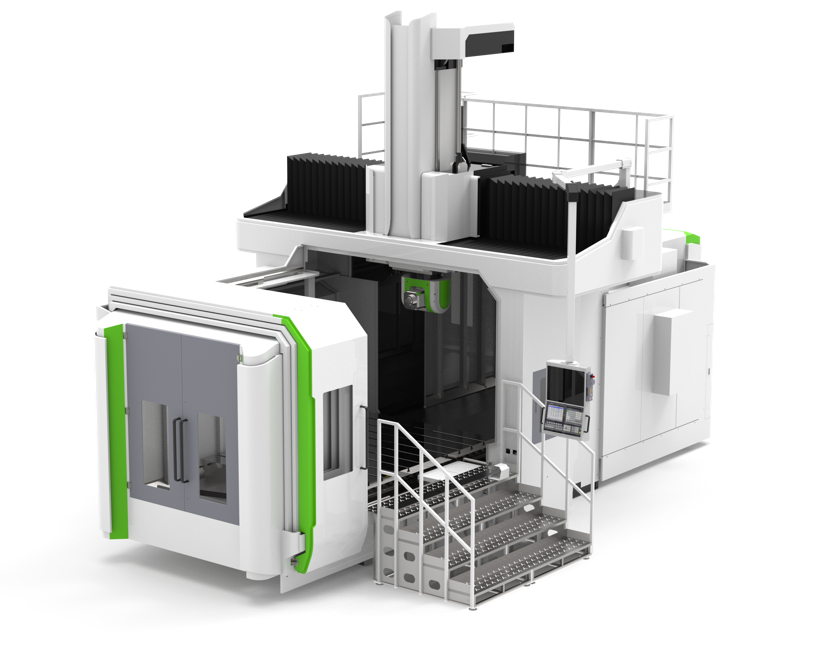
Esempio di una fresatrice Gantry (Hartford HSA-423)
Il portale (detto anche ponte o gantry) è una struttura a doppia colonna con traversa che sostiene il mandrino; il letto, invece, costituisce il piano su cui è fissato il componente in lavorazione. Date le dimensioni notevoli del letto e del grezzo non è possibile alloggiare gli assi rotatori sulla tavola poichè la massa da ruotare sarebbe eccessiva e complessa da gestire, qualora siano presenti gli assi di rotazione è necessario montarli a ridosso del mandrino in modo da conferire la rotazione all’utensile. La struttura a portale inoltre permette alla fresatrice di muoversi attorno al componente lavorato senza troppi problemi di ingombro. Esistono poi due varianti di questa fresatrice: a portale e a portale mobile. Mentre nel primo caso il moto di traslazione lungo la direzione longitudinale è data al pezzo, nel secondo caso, invece, la traslazione nella medesima direzione è data direttamente alla struttura a portale, che alloggia su delle guide motorizzate. Il moto trasversale, invece, in entrambe le tipologie è dato al mandrino che si muove lungo la traversa del portale. Un esempio di fresatrice a portale fisso è la Hartford HSA-423.
Applicazione: Lavorazione di componenti di considerevoli dimensioni e massa.
TORNIO A 2 ASSI
Il tornio a 2 assi è la tipologia più semplice di tornio CNC presente sul mercato. I 2 assi di traslazione sono in questo caso l’asse X e l’asse Z. Il primo è perpendicolare all’asse di rotazione del pezzo, dunque, muove radialmente la torretta di lavorazione mentre l’asse Z è parallelo all’asse di rotazione e trasla la torretta in direzione longitudinale. Un esempio di tornio a 2 assi è l’Okuma GENOS L3000-E. Questa configurazione relativamente semplice della macchina le permette di essere economica ma di mantenere un’elevata produttività.
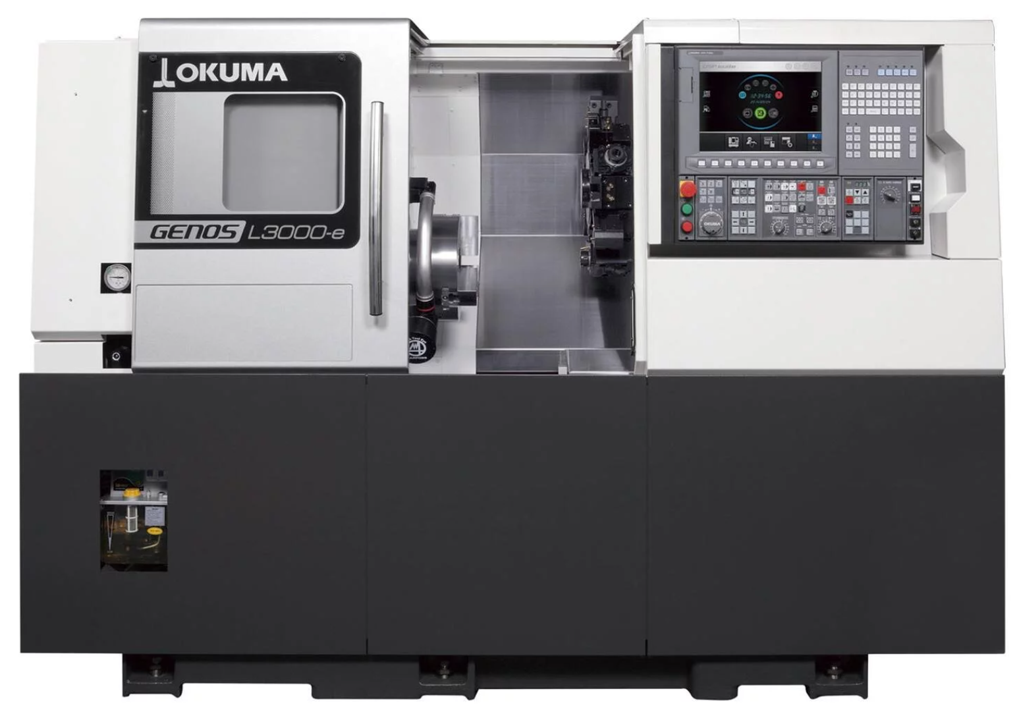
Esempio di un tornio a 2 assi (Okuma GENOS L3000-E)
Applicazione: Realizzazione di componenti assialsimmetrici.
TORNIO A 3 ASSI
Il tornio a 3 assi, rispetto a quello a 2, possiede un terzo asse chiamato Y. La presenza di questo asse permette di avere una completa capacità di movimento in direzione radiale rispetto all’asse di rotazione del pezzo. In questo modo è possibile effettuare oltre che semplici operazioni di tornitura e foratura anche operazione di fresatura. Questo è possibile delle torrette motorizate e degli appositi portautensili dotati di trasmissione. Essi sono in grado di conferire la rotazione alla fresa o alla punta erogando potenza e coppia così da permettere l’asportazione di materiale.
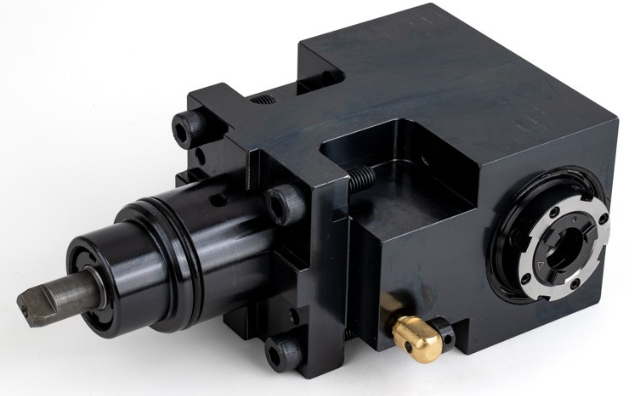
Esempio di un portautensili con trasmissione per tornio modello Haas BMT45
Un esempio di tornio a 3 assi è l’Okuma GENOS L3000-E con l’aggiunta dell’asse Y opzionale. In questo modo, la macchina diventa di gran lunga più versatile e permette di effettuare anche lavorazioni per fresatura.
Applicazione: Realizzazione di componenti assialsimmetrici o con semplici geometrie prismatiche con l’aggiunta di features realizzate mediante fresatura.
TORNIO MULTI-TORRETTA
Il tornio multi-torretta presenta più torrette portautensili, ognuna delle quali, nella maggioranza dei casi, ha 2 o 3 gradi di libertà rispetto al grezzo e permette di effettuare più lavorazioni contemporaneamente. Un esempio di tornio multi-torretta è l’Okuma LT3000 o la serie TTL di CMS. Il vantaggio maggiore che si ha nell’utilizzo di questa configurazione è l’aumento della produttività. L’aspetto più competitivo della macchina consiste nella possibilità di lavorare in parallelo e di compiere diverse operazioni contemporaneamente sullo stesso pezzo. Si presta dunque all’applicazione in produzioni ad alto volume e situazioni in cui l’investimento può essere ammortizzato con l’incremento di produttività. In genere i prodotti lavorati su queste macchine sono prodotti in serie che prevedono la realizzazione di batch di grandi dimensioni dello stesso componente. In genere i torni multi-torretta hanno due torrette che possono lavorare in simultanea e in più presentano contropunto motorizzata.
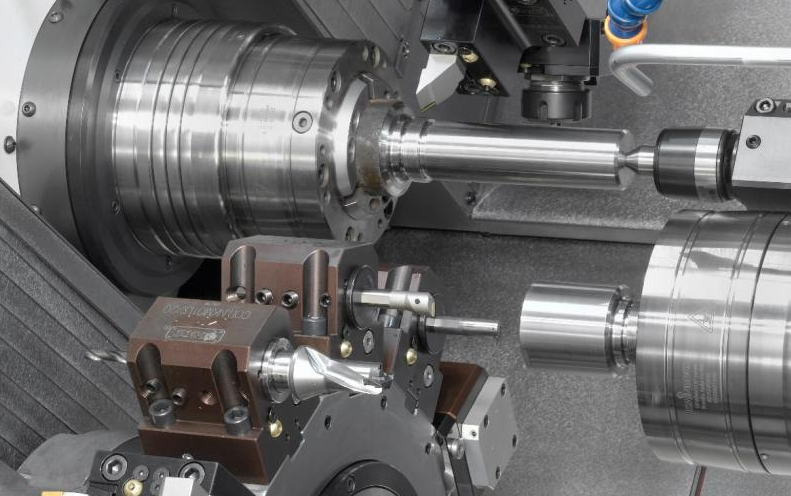
Esempio dell’area di lavoro di un tornio multi torretta CMS serie TTL
Applicazione: Realizzazione di componenti lunghi e complessi che richiedono un’ingente quantità di rimozione materiale. Lavorazione di pezzi piccoli in cui è possibile dividere le operazioni tra le torrette per ridurre drasticamente il tempo ciclo.
TORNIO A FANTINA MOBILE
Il tornio a fantina mobile è una macchina particolare la cui architettura si discosta da quella di un tornio classico. La principale peculiarità di un fantina mobile sta nell’associare il moto di avanzamento, quindi longitudinale, non più all’utensile bensì al grezzo.
Il tornio svizzero nasce dalla necessità di ricavare molteplici componenti in serie da singole barre di lunghe dimensioni. La necessità dunque è quella di avere la possibilità di addurre in continuazione materiale in zona di lavoro senza dover ricorrere a continui staffaggi di barre più corte.
Nella figura qui sotto viene schematizzato un tornio svizzero. Come si può vedere la barra, che in questo caso è caricata da destra verso sinistra, viene spinta dalla fantina mobile attraverso una boccola chiamata bussola di guida la cui funzione è quella di mantenere il sistema rigido. Entrata nell’area di lavoro la barra viene lavorata dagli uTensili che sono fissati al telaio e che si muovo in direzione radiale per asportare materiale.
Un esempio di tornio a fantina mobile può essere individuato nello Star SW-20.
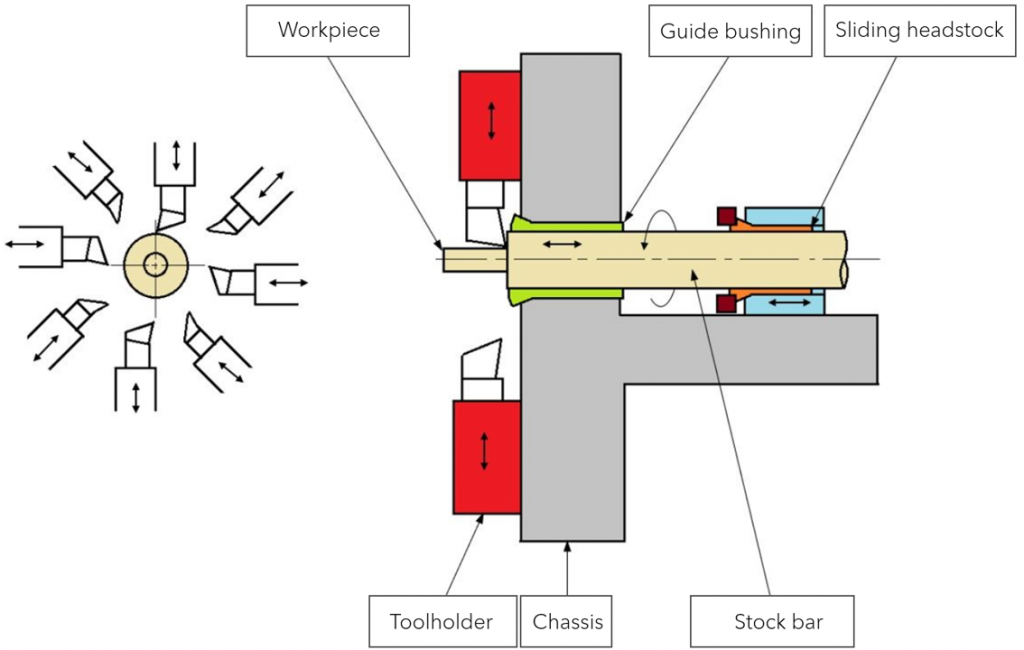
Schema di un tornio a fantina mobile
Applicazione: Realizzazione di componenti generalmente piccoli ed in lotti di grandi dimensioni (viteria, componenti per orologi ecc…).
TORNIO VERTICALE
Questo tornio lavora come un tornio convenzionale ma l’asse di rotazione del pezzo non è orizzontale ma verticale. Questa configurazione viene usata principalmente per la realizzazione di componenti pesanti e dal grande diametro (e.g. le ruote dei treni) il cui bloccaggio su morsa orizzontale genererebbe momenti e sollecitazioni a taglio insostenibili dalla macchina.
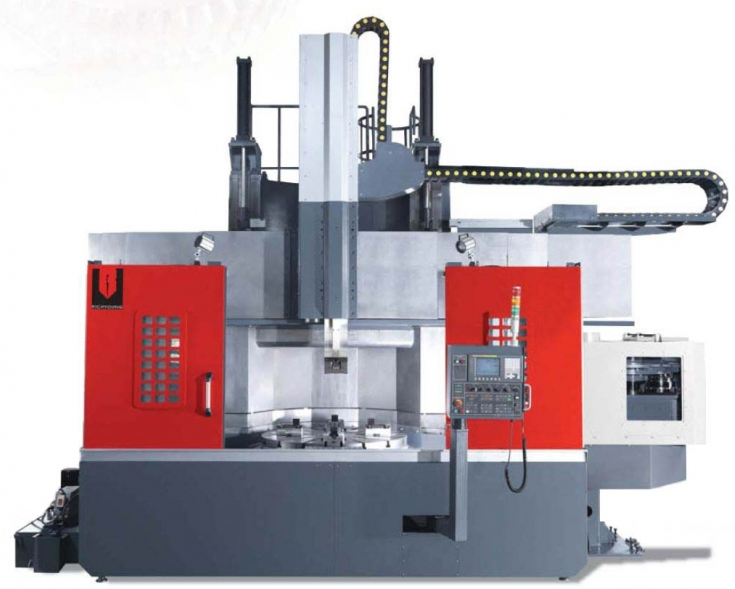
Esempio di un tornio orizzontale (RIC-DV3000)
Applicazione: Lavorazione di componenti di diametri importanti con considerevole massa.
CENTRO MULTIFUNZIONE
Un centro di lavorazione multifunzione è una tipologia di macchina in grado di svolgere diverse operazioni senza la necessità di un cambio di set-up. In generale, un centro multifunzione è in grado di svolgere operazioni sia di tornitura sia di fresatura senza che vi sia alcuna azione di riposizionamento del grezzo o di cambio macchina tra una lavorazione e l’altra.
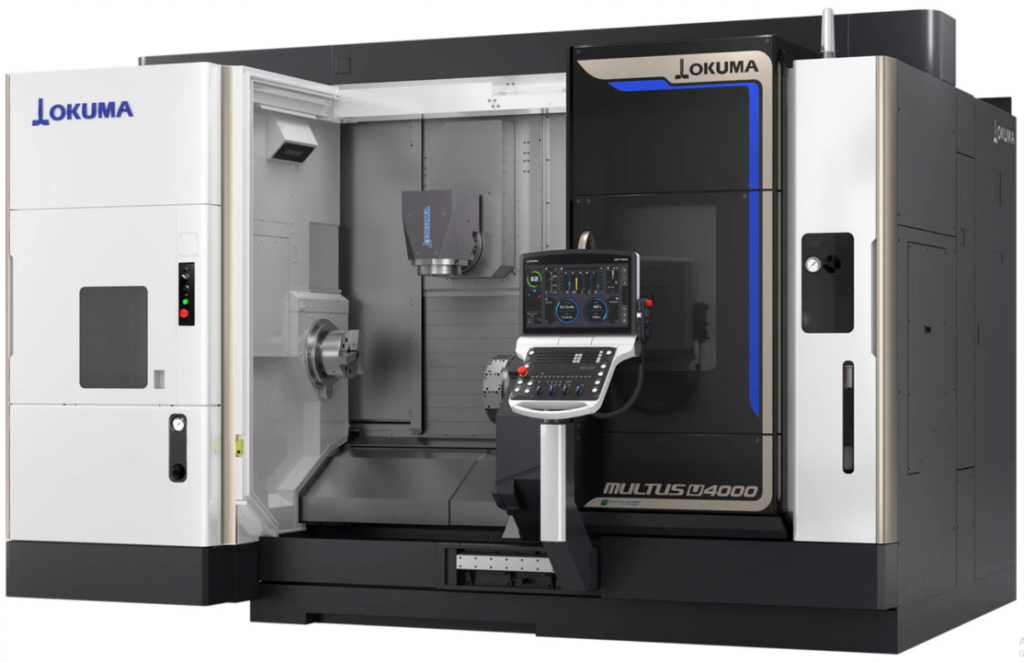
Esempio di un centro multifunzione (Okuma MULTUS U4000)
Esistono centri di lavorazione multifunzione con diversa disposizione al loro interno. Ad esempio, nell’Okuma MULTUS U4000 si ha un mandrino con punta e contro punta con asse di rotazione orizzontale come in un tornio tradizionale ma si ha anche un mandrino per fresatura. La peculiarità di questa macchina è che questo secondo mandrino può funzionare sia staticamente come torretta porta utensile sia da mandrino vero e proprio e realizzare feature da tornio-fresatura o fresatura pura.
Un’altra disposizione può essere quella della IBARMIA ZVH 55 in cui la rotazione per la tornitura è data dalla rotazione della tavola attorno all’asse verticale come avviene per un tornio verticale.
I vantaggi portati dall’adozione di questa soluzione sono molteplici:
- Risparmio in termini di tempo e manodopera dovuti all’assenza di ripiazzamenti del pezzo tra una lavorazione e l’altra permettendo di ottenere il prodotto finito con un unico set-up su un’unica macchina
- Risparmio di spazio in quanto una macchina svolge le funzioni che tradizionalmente sono associate a due macchine differenti (tornio e fresatrice)
- Migliore precisione in quanto il singolo piazzamento del pezzo riduce le fonti di errore.
- COMPETENZE ACQUISITE
Hai acquisito le seguenti competenze:
- Capire le principali funzioni degli organi che compongono una macchina CNC.
- Riconoscere le principali tipologie di macchine CNC
- Riconoscere le loro prinicpali caratteristiche cinematiche
- Eseguire una prima scelta della configurazione di macchina in funzione dei pezzi da lavorare
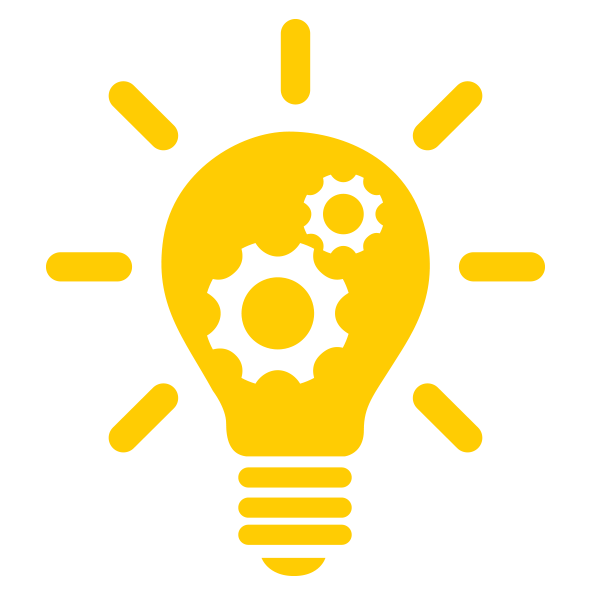
CONTATTI UTILI, LINK E DOWNLOAD
Contatti
- Per gli studenti:
Prof. Annoni Massimiliano, Politecnico di Milano: massimiliano.annoni@polimi.it - Per gli educatori:
Prof. Annoni Massimiliano, Politecnico di Milano: massimiliano.annoni@polimi.it - Per le imprese:
Prof. Annoni Massimiliano, Politecnico di Milano: massimiliano.annoni@polimi.it
Ufficio marketing, Celada Spa: marketing@celadagroup.com
Link Utili
- LEARNING TIME: -- min.